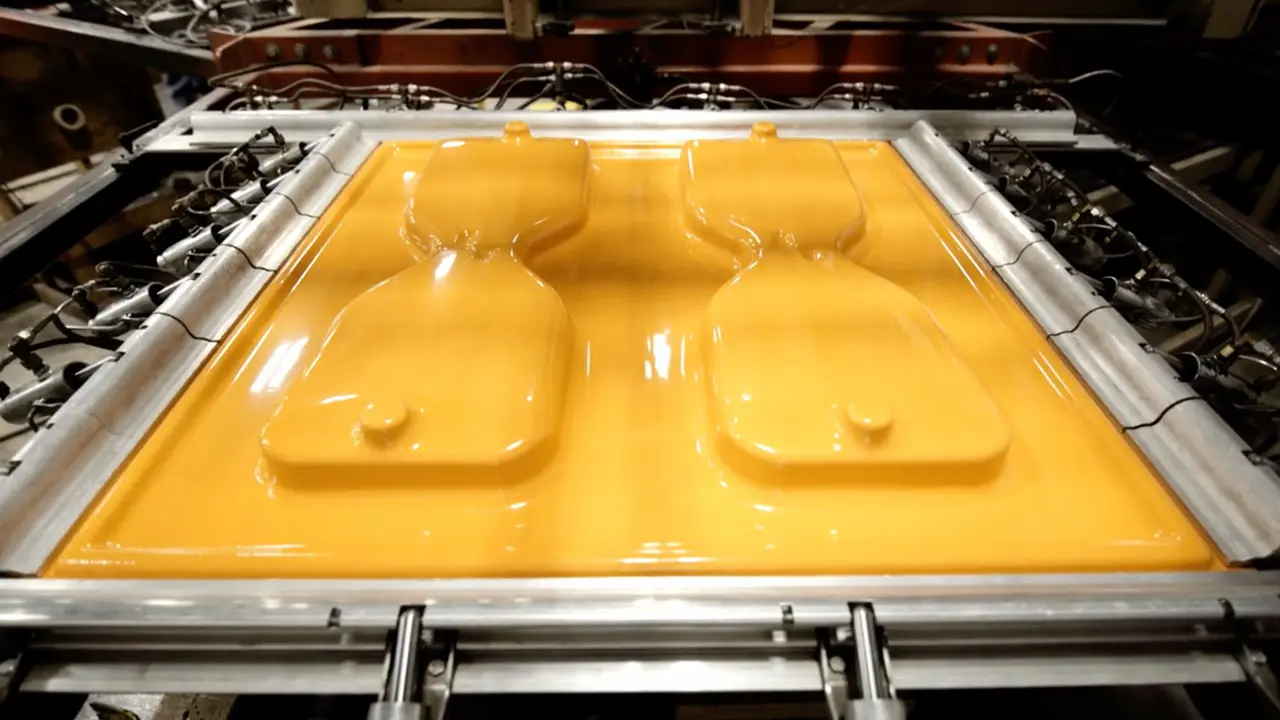
Rotational Moulding
Rotational moulding vs. vacuum formingDo you want to have a plastic product manufactured and are you hesitating between rotational moulding and vacuum forming? Both production techniques have their own advantages, depending on the design, batch size and desired properties. Pentas specialises in rotational moulding, but we understand that not every product is suitable for this. Vacuum forming is an alternative production method with different characteristics and advantages. In this article, we compare both techniques so you can better determine which method is most suitable for your product.