Materials for Rotational Moulding
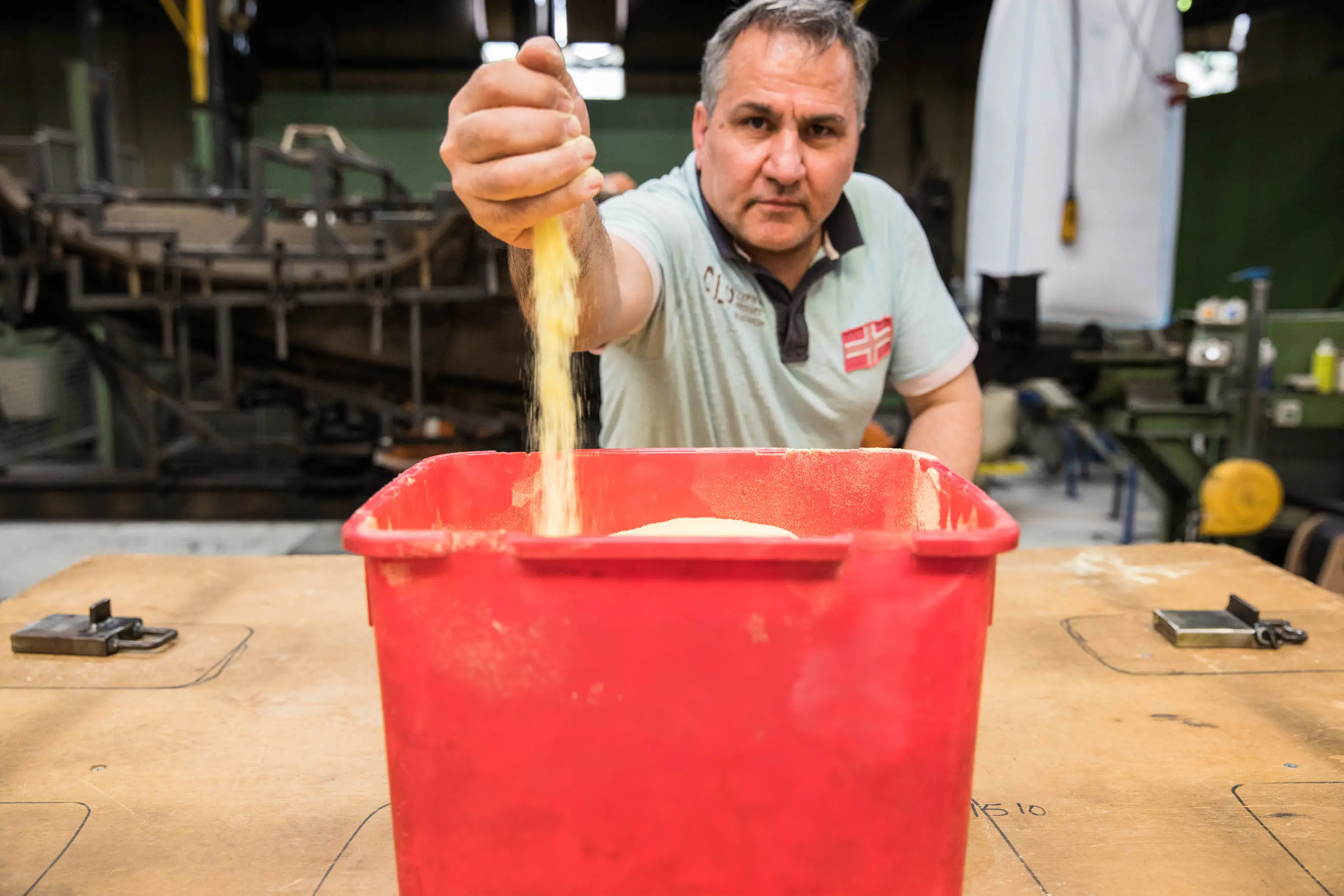
Rotational moulding is a popular choice for a wide range of applications. In this article, we discuss the various materials used in rotational moulding, their properties, and the factors influencing the choice of material for specific applications.
Table of contents
Polyethylene (PE)
Polyethylene is known as the most prominent material in rotational moulding, accounting for 84% of the market. The versatility of polyethylene is due to its availability in different densities, each with its own advantages. LDPE (low-density polyethylene) is known for its flexibility, LLDPE (linear low-density polyethylene) for its impact resistance, and HDPE (high-density polyethylene) for its high stiffness, making it suitable for products requiring structural strength, such as large containers and industrial housings.
All these variants share excellent chemical resistance and durability, which are essential in numerous applications. However, the innovation does not stop here. In collaboration with LyondellBasell, we have introduced a new polyethylene material: Icorene 1490. This medium-density linear polyethylene is not only more energy-efficient in the melting process but also improves the quality and efficiency of our production.
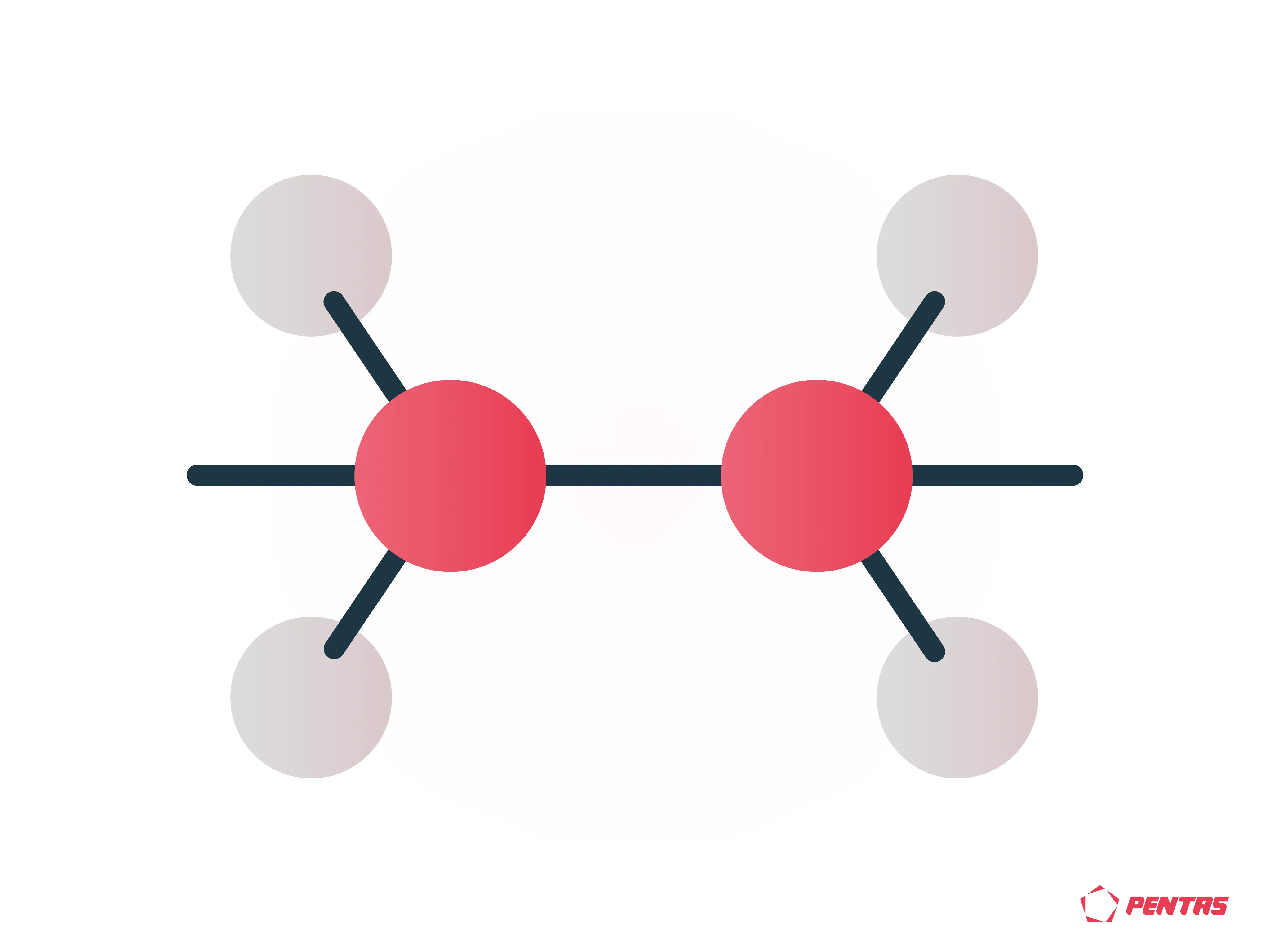
Icorene 1490 stands out for its impressive resistance to stress cracking and maintains its integrity even at temperatures down to -40°C. These properties make the material particularly attractive for applications that require both durability and environmental friendliness.
Polypropylene (PP)
Polypropylene is known for its excellent chemical resistance and high melting temperature, making it ideal for medical and laboratory equipment that needs to be sterilised. PP is also popular in the automotive sector for parts that can withstand high temperatures. Although PP is harder to mould than polyethylene, it offers better performance at higher temperatures and has higher stiffness.
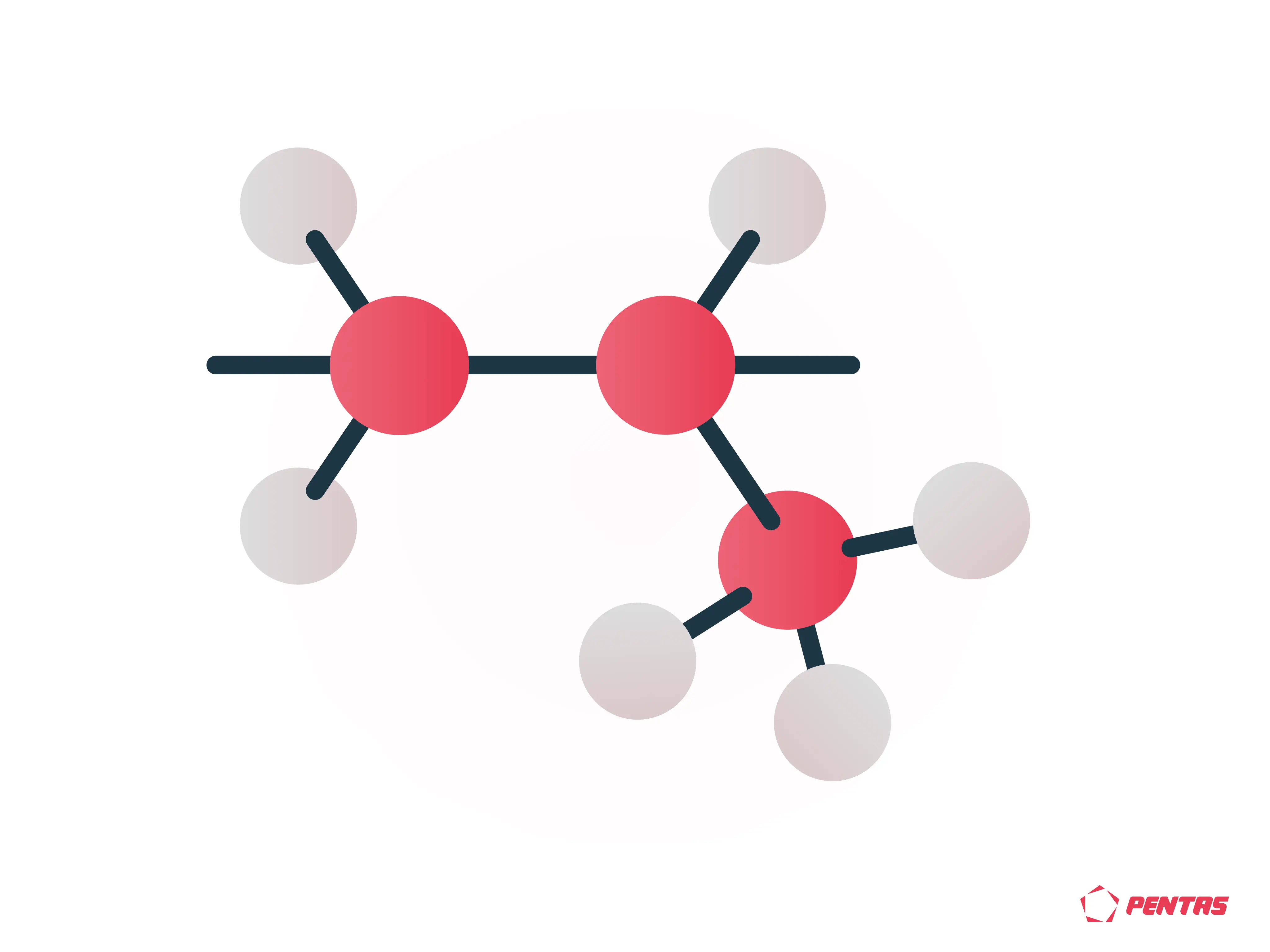
Polycarbonate and Polyvinyl Chloride (PVC)
Polycarbonate is valued for its clarity and impact resistance, making it an excellent choice for transparent applications like security housings and medical devices. PVC, on the other hand, offers flexibility and is a good choice for products requiring both strength and pliability, such as hoses and seals. Both materials require specific processing conditions due to their unique properties and are generally more expensive than PE.
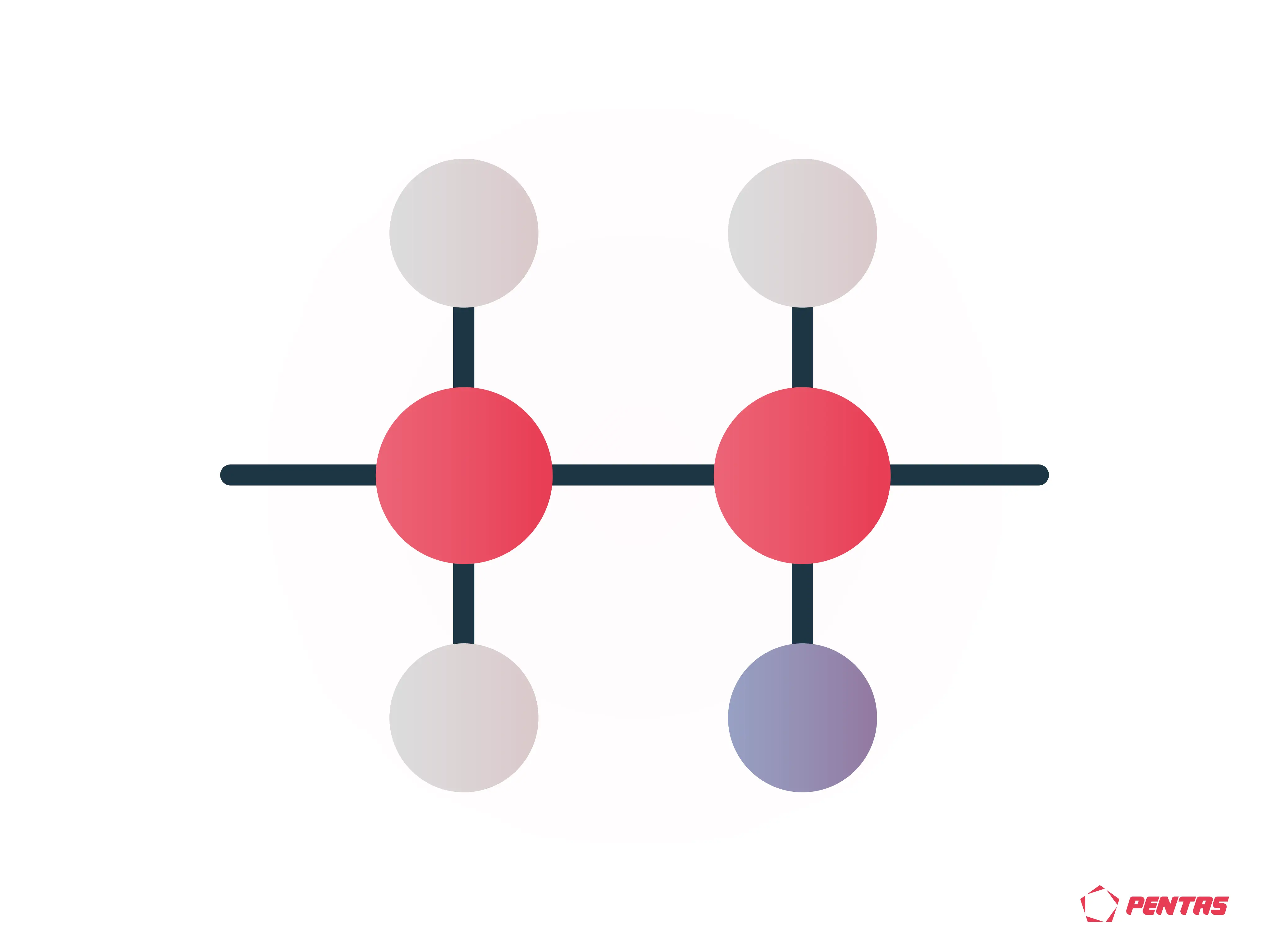
Polyamide (PA)
PA6 (Polyamide 6) and PA12 (Polyamide 12) are both types of polyamide, better known as nylon. They are widely used in various applications due to their excellent mechanical properties and chemical resistance.
Polyamide 6 (PA6)
PA6 is known for its excellent mechanical strength and rigidity. A significant aspect of PA6 is its ability to absorb moisture. While this can be a disadvantage in some environments, as it can affect the mechanical properties and dimensional stability, PA6 has a higher absorption rate than PA12, which requires careful consideration in applications where long-term exposure to moisture occurs. Additionally, PA6 is easier to process than PA12, resulting in lower production costs.
Applications:
Due to its robustness, PA6 is often used in the automotive industry, for machine parts, and in electronics.
Polyamide 6 ook wel bekend als PA6.
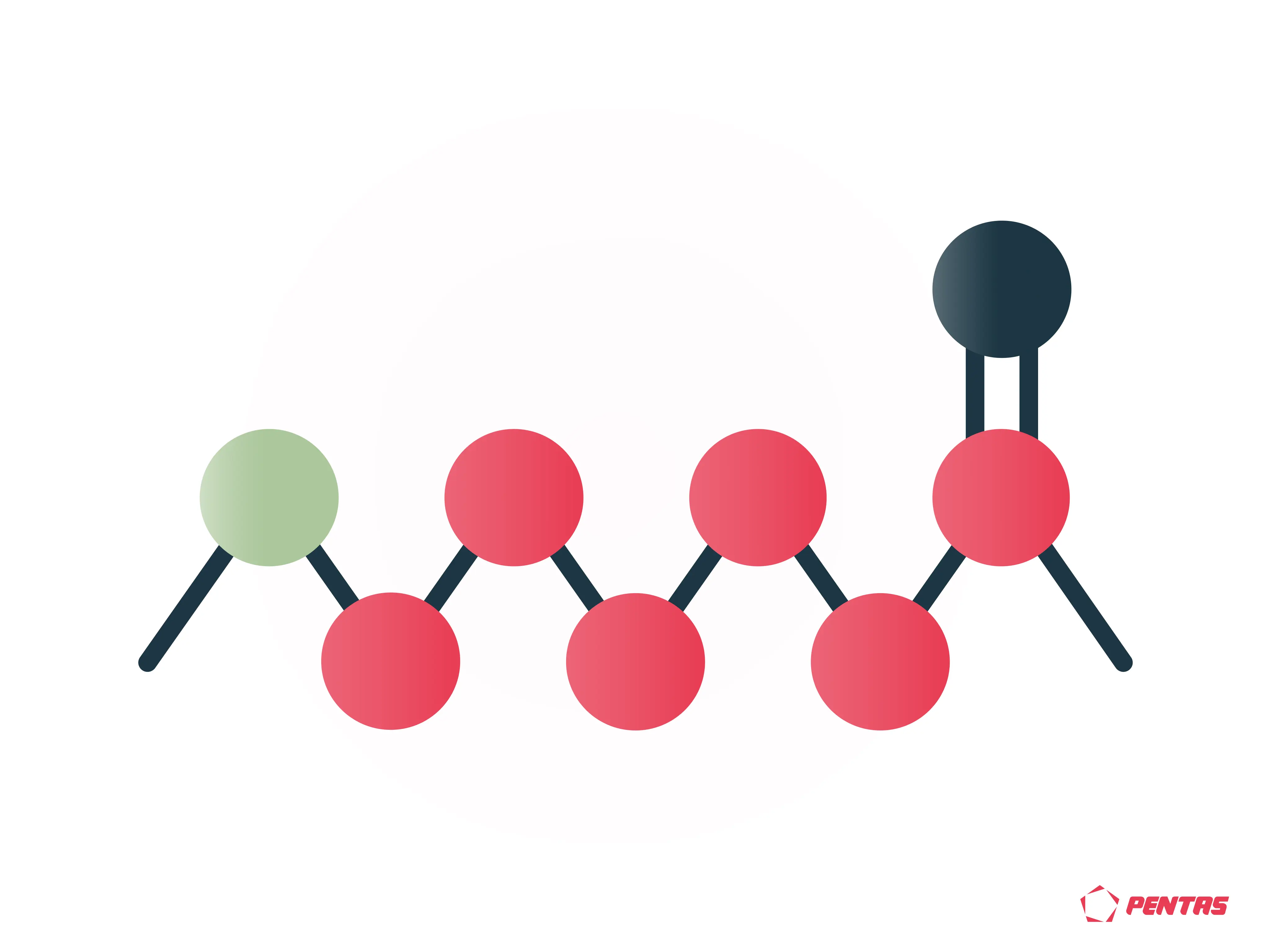
Polyamide 12 (PA12)
PA12 is known for its excellent chemical resistance, particularly against oils, fats, and fuels. Furthermore, PA12 has lower moisture absorption compared to PA6, leading to better dimensional stability and more consistent mechanical properties under varying environmental conditions. Additionally, PA12 offers greater flexibility than PA6 and performs well at low temperatures.
Applications:
PA12 is frequently used in the production of fuel lines, pneumatic tubing, and other applications requiring chemical resistance and dimensional stability.
Factors in Material Choice
Choosing the right rotational moulding material depends on the specific requirements of the application, such as the need for strength, flexibility, and resistance to moisture and chemicals.
Here are some key factors to consider:
The choice of a specific rotational moulding material depends on a combination of factors, including required mechanical properties, chemical resistance, temperature resistance, and cost. Understanding these properties in relation to the application is crucial for successfully designing and producing rotationally moulded products.