The future of rotational moulding
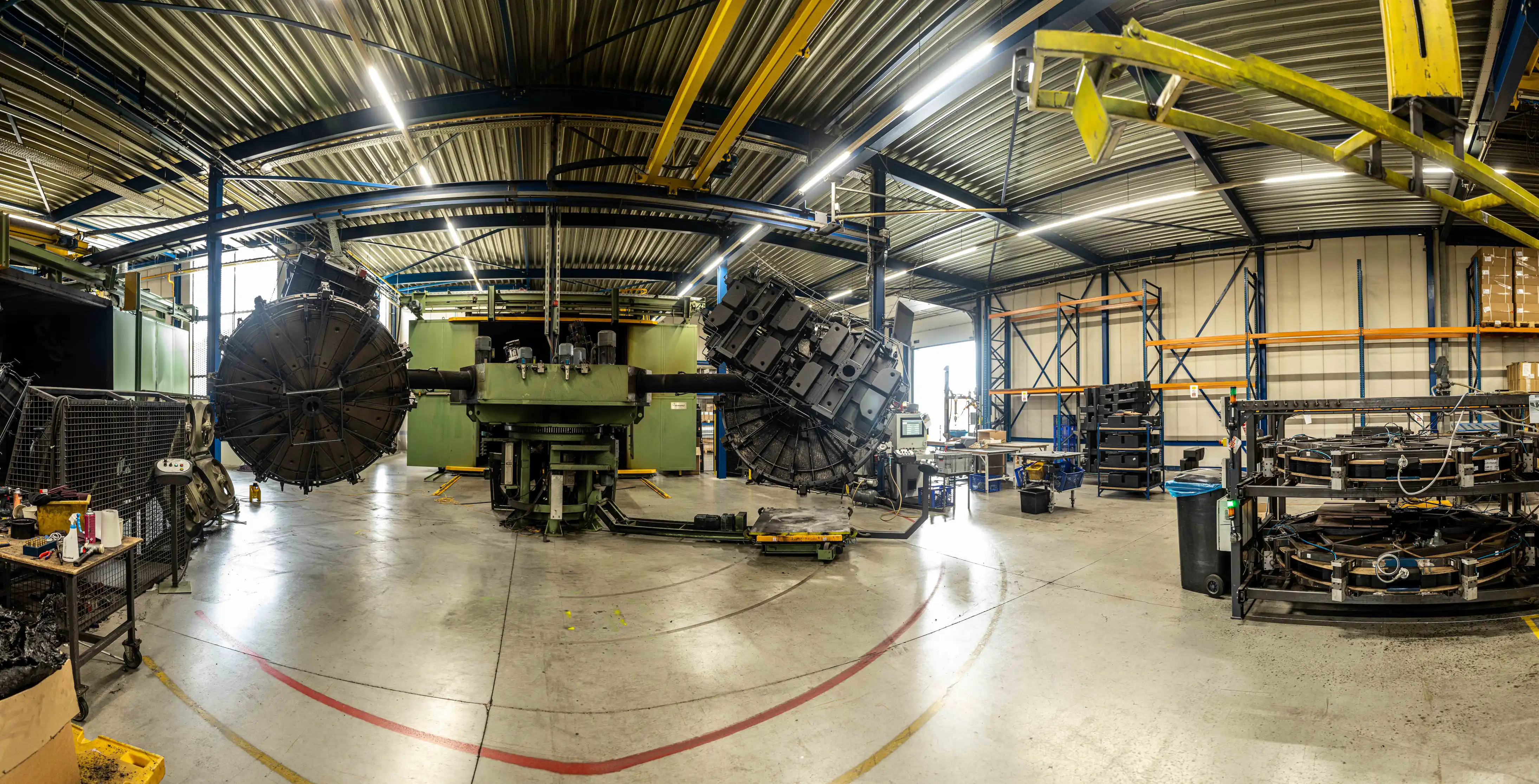
The future of rotational moulding will be driven by technological advancements and the growing demand for sustainable production methods. In this blog, we look at the developments, recent trends, and innovations within the industry.
Table of contents
Sustainability and recycling
Rotational moulding is expected to increasingly focus on sustainability, emphasizing the recycling of materials. Companies will use more recycled plastics in their production processes, driven by both environmental considerations and economic benefits. Technology will evolve to process a wider range of recycled materials while maintaining the quality and integrity of the end product.
Transition to electric and hydrogen
In the future, we will see a shift from fossil fuels to electric and hydrogen energy sources. This transition is essential to reduce the ecological footprint of rotational moulding and promote efficiency and cost savings in the long term.
A significant innovation in this development is the SMART-machine van Persico and Robomould van AMS. These machines illustrate a new approach to sustainability and efficiency in the rotational moulding process by using electricity for heating. This results in significant reductions in energy consumption and emissions.
However, we must acknowledge that this transition also brings significant challenges. For example, switching from a gas-fired oven to an electric oven requires substantial additional capacity on the power grid. In the Netherlands, this is a limiting factor until 2030. Furthermore, gas remains a primary energy carrier particularly suitable for heating processes within our production. Much of the energy we use daily is generated from fossil fuels. This conversion results in significant energy losses, making the remaining energy only a fraction of the original energy source, rendering the conversion to heat an inefficient step for now.
While the path to a more sustainable industry is challenging, it is essential to continue innovating and seeking sustainable solutions that are both ecologically and economically beneficial for the sector. The journey to a greener future is complex, but with dedication and innovation, we can achieve significant improvements.
Introduction of new materials
The introduction of new heating techniques for moulds plays a significant role in using new materials, which are essential for recycling and innovating within the sector. Advanced process control with electrically heated molds, which are not placed in a hot oven, allows for the use of different materials and broadens the spectrum of manufacturable products. This progress also enables various tools, such as dropbox and vacuum systems, to be built directly on the mould, making the production process more efficient. This not only increases the versatility of the end product but also achieves a higher level of process control and material innovation.
Further automation
Robotic technology is becoming more accessible and therefore applicable for smaller series. This means that we will increasingly use Robots for repetitive tasks in the rotational moulding market. But it has more advantages:
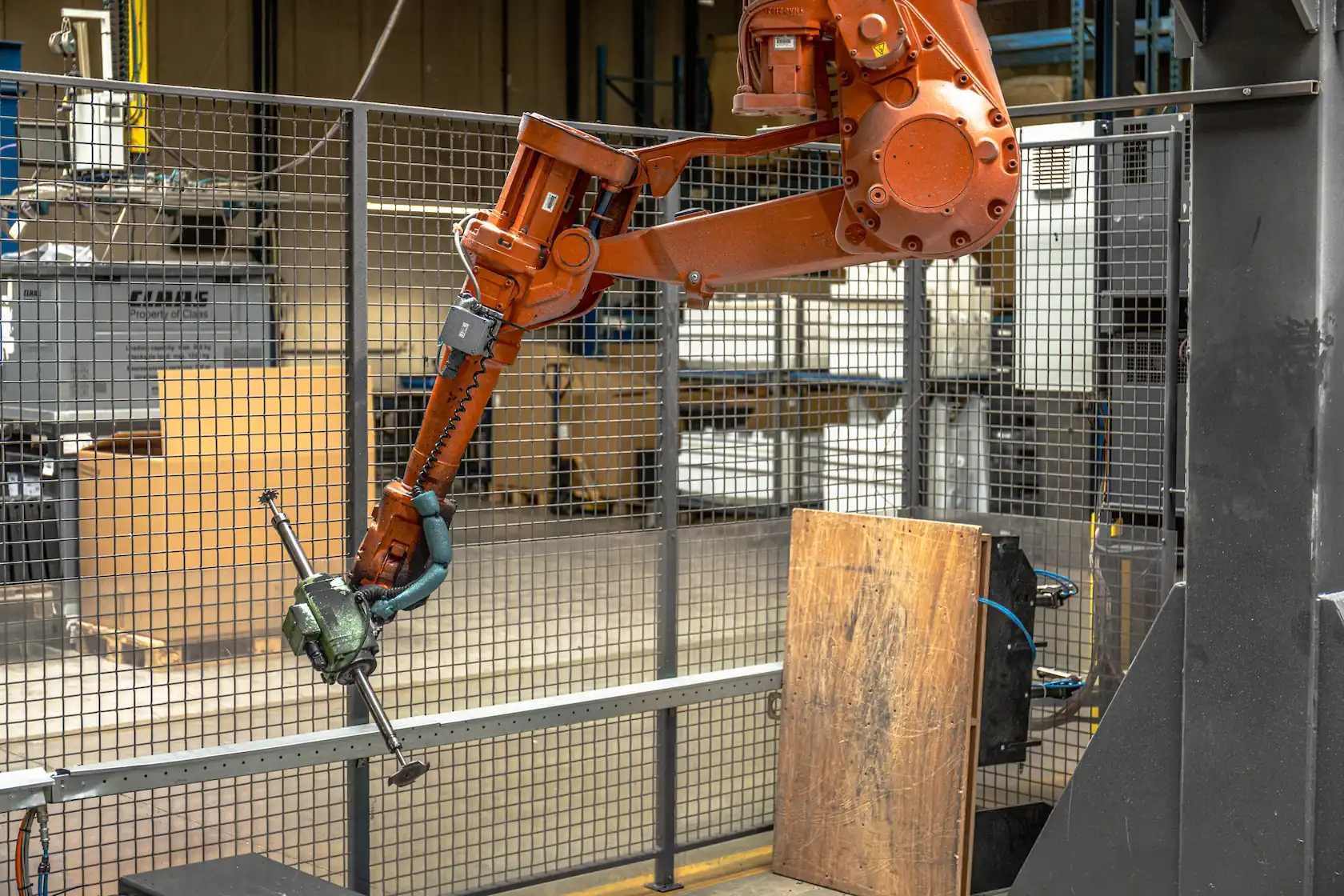
The integration of robotic technology in the rotational moulding industry is thus a promising development that improves both operational efficiency and product quality while keeping the industry flexible in offering products that meet specific customer needs.
Integration of AI in industry 4.0
The integration of AI ensures even more innovative smart products. This development enables us to equip machines and devices with advanced sensors and communication technologies, allowing them to connect with IoT platforms (Internet of Things). This enables real-time monitoring and control of the production process, leading to increased efficiency. Ultimately, with all this data, we can make predictions and set up autonomous planning.
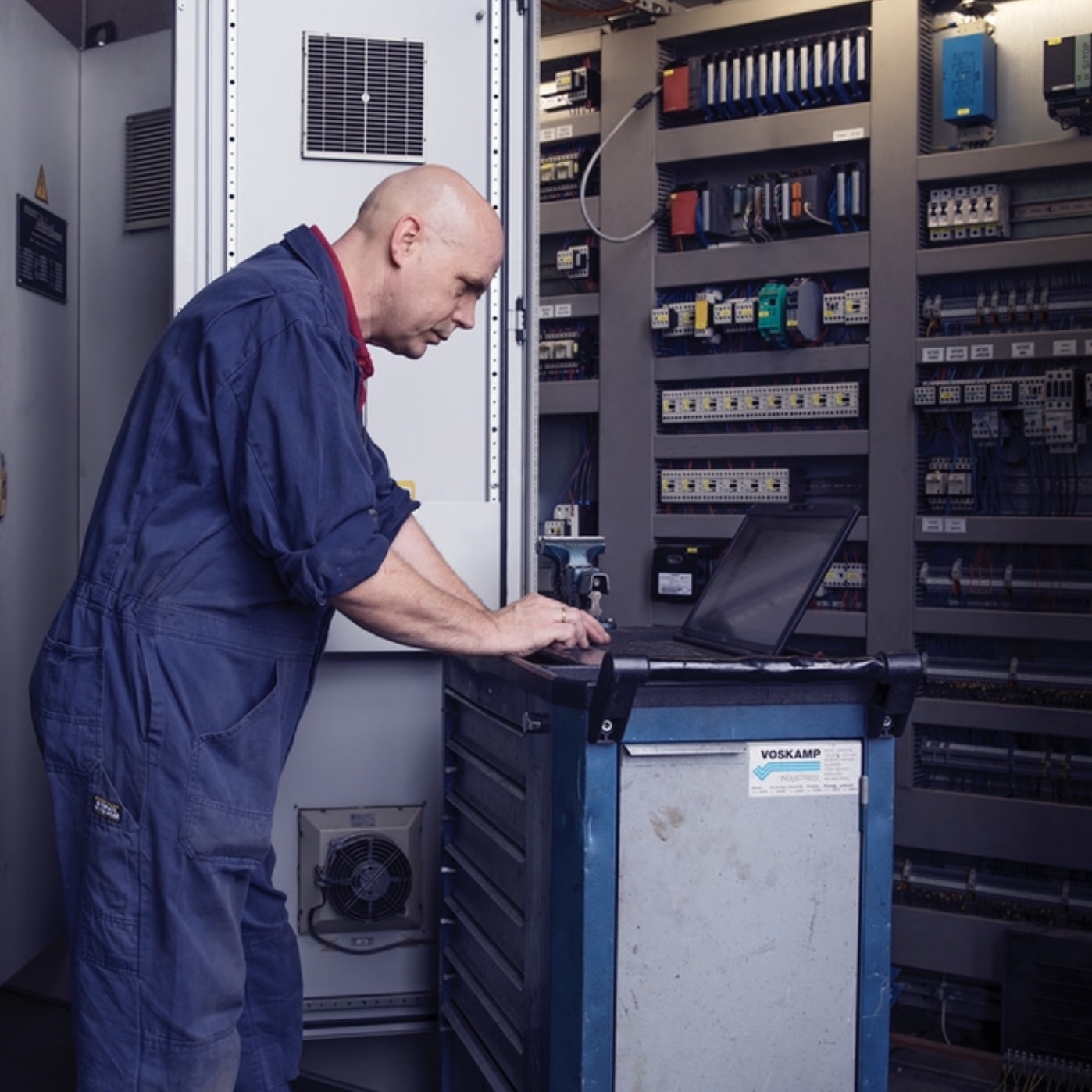
All in all, the future of rotational moulding is promising, with advancements in sustainability, material use, technology integration, and customization. These developments will contribute to improving efficiency, sustainability, and production processes.