Rotatiegieten vs. Vacuümvormen: Welke productietechniek past het beste bij jouw project?
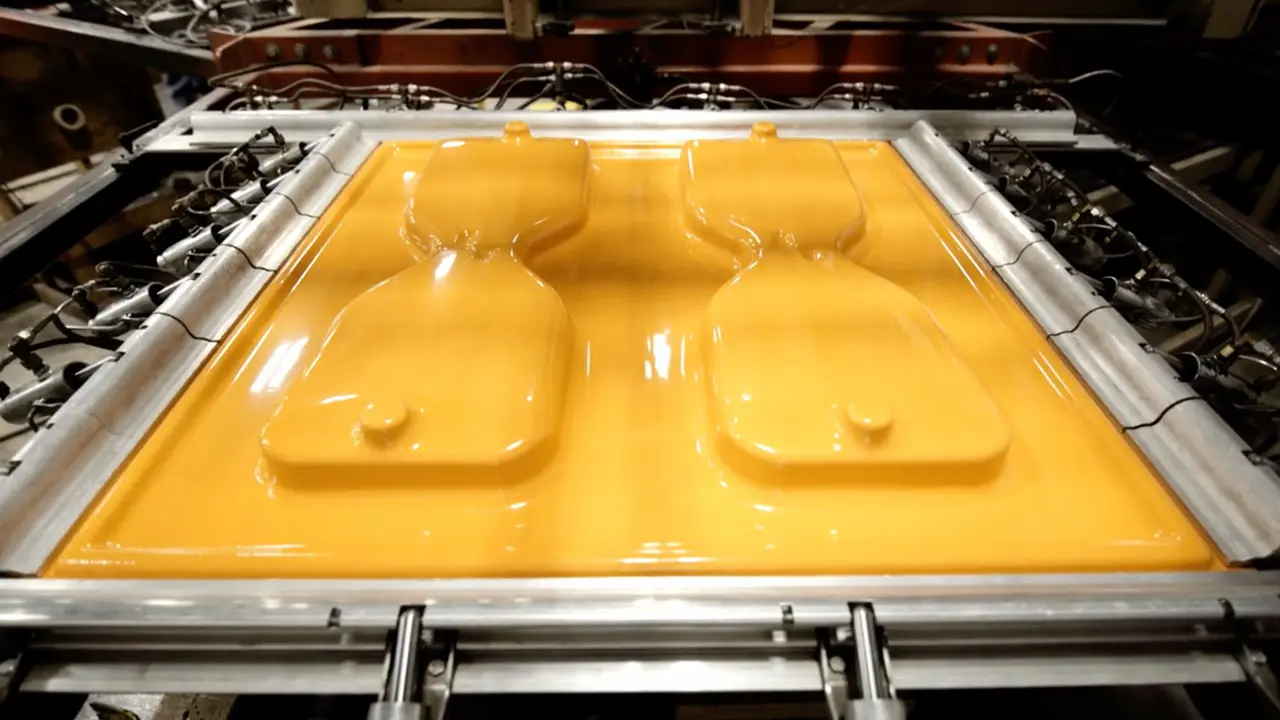
Wil je een kunststof product laten maken en twijfel je tussen rotatiegieten en vacuümvormen? Beide productietechnieken hebben hun eigen voordelen, afhankelijk van het ontwerp, de seriegrootte en de gewenste eigenschappen. Pentas is specialist in rotatiegieten, maar wij snappen dat niet elk product zich hiervoor leent. Vacuümvormen is een alternatieve productiemethode met andere kenmerken en voordelen. In dit artikel vergelijken we beide technieken, zodat je beter kunt bepalen welke methode het meest geschikt is voor jouw product.
Table of contents
Wat is vacuümvormen?
Vacuümvormen is een productiemethode waarbij een kunststof plaat (thermoplast) wordt verhit tot deze vervormbaar is en vervolgens met behulp van vacuüm over een mal wordt getrokken. Hierdoor neemt het materiaal de vorm van de mal aan. Eenmaal afgekoeld behoudt het plastic deze vorm, waardoor het gewenste onderdeel ontstaat. Deze techniek wordt toegepast op uiteenlopende producten, van verpakkingsblisters tot machinebehuizingen en interieurpanelen.
Het vacuümvormproces verloopt in vier stappen:
Verwarmen van de kunststofplaat: Een vlakke thermoplastische kunststof plaat (bijvoorbeeld ABS of PETG) wordt vastgeklemd en geleidelijk verhit tot hij zacht en vervormbaar is.
Vormgeven over de mal: De warme plaat wordt over de mal geplaatst. Vervolgens wordt de lucht tussen de plaat en de mal weggezogen, zodat de kunststof plaat strak tegen de contouren van de mal trekt. De kunststof volgt hierdoor precies de vorm van de mal.
Afkoelen: Terwijl het vacuüm behouden blijft, koelt de gevormde kunststof af. De plaat hardt uit in de nieuwe vorm en behoudt deze na het afkoelen. Koelventilatoren kunnen hierbij worden gebruikt om het proces te versnellen.
Losnemen en afwerken: Het uitgeharde product wordt uit de mal gehaald. Overtollig materiaal, zoals randen of het stuk plaat rondom het product, wordt weggesneden of gefreesd. Eventuele nabewerking (bijv. gaten boren of uitsnijden) vindt in deze fase plaats om het onderdeel gebruiksklaar te maken.
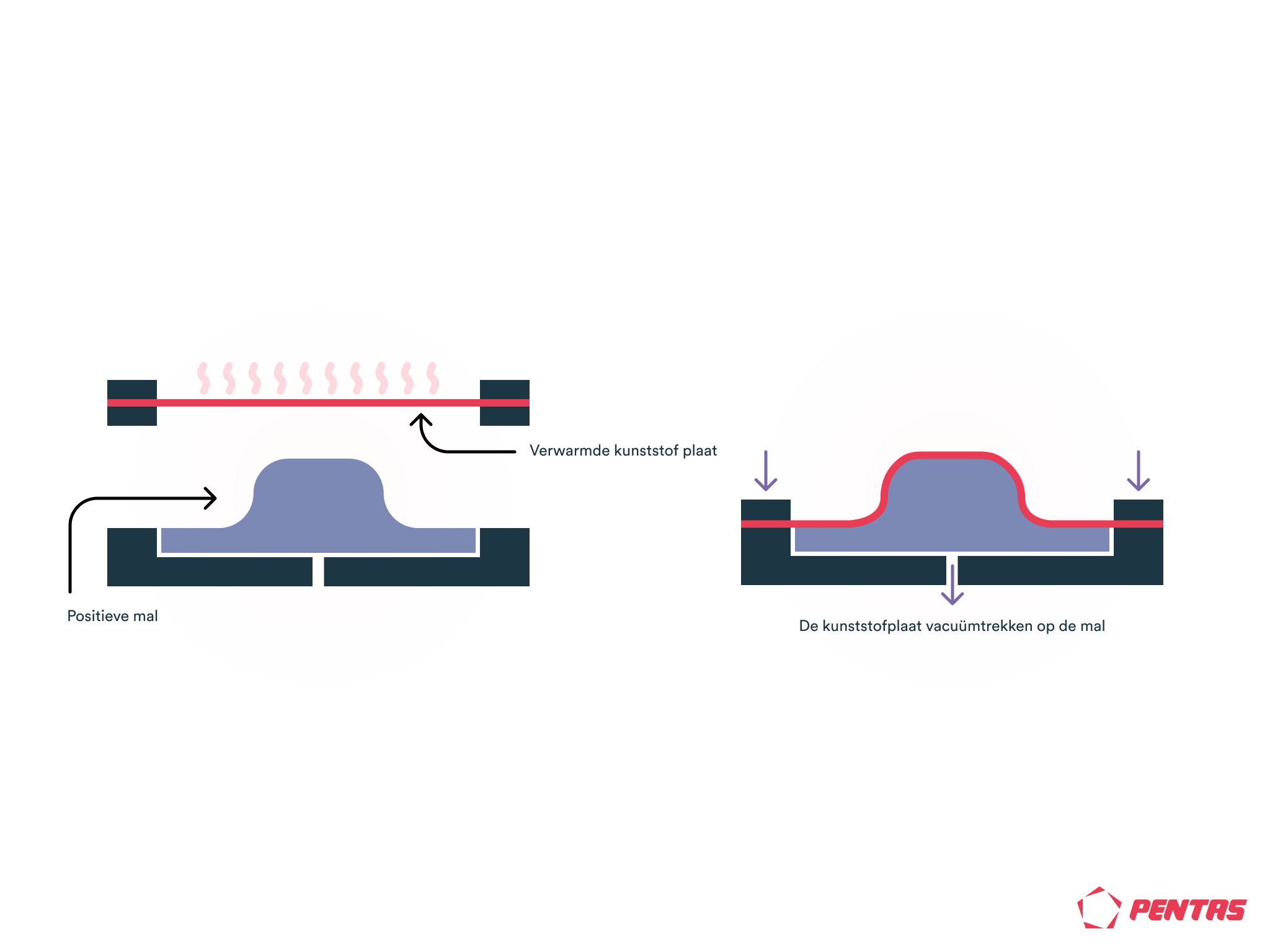
Een van de grootste voordelen van vacuümvormen is de lage investeringsdrempel voor nieuwe producten. De matrijskosten zijn laag, vooral vergeleken met spuitgieten of blaasvormen. Dit maakt de techniek aantrekkelijk voor kleine series, prototypen en maatwerkproducten. Daarnaast kunnen met vacuümvormen relatief grote kunststof producten worden gemaakt (afhankelijk van de machine, vaak tot enkele meters). Er is een brede materiaalkeuze: veel thermoplasten zoals ABS, polystyreen, PET, PVC en polycarbonaat zijn geschikt. Ook zijn de cyclustijden korter dan bij bijvoorbeeld rotatiegieten, waardoor bij serieproductie de kosten per stuk laag gehouden kunnen worden. Vacuümvormen is daardoor een kosteneffectieve methode voor zowel kleine oplagen als grotere series.
Toch zijn er beperkingen. De ontwerpvrijheid is beperkter dan bij rotatiegieten of spuitgieten; complexe of zeer diepe vormen met ondersnijdingen zijn lastig te realiseren met vacuümvormen. Doordat het materiaal tijdens het vormen wordt uitgerekt, kunnen er wanddikte verschillen optreden in het product (dunnere gedeeltes op sterk gerekte plekken). Verder ontstaat er relatief veel restmateriaal rondom het product dat na het vormen moet worden weggesneden. Ten slotte kunnen in vacuümgevormde producten geen integrale details zoals schroefdraad en complexe ribben worden meegevormd; zulke functies moeten later worden toegevoegd (bijvoorbeeld door frezen of montage). Ondanks deze beperkingen is vacuümvormen een zeer veelzijdige techniek voor allerlei toepassingen waar een relatief eenvoudige vorm volstaat.
Toepassingen van vacuümvormen:
Vacuümvormen komt vooral tot zijn recht bij de productie van grotere kunststof behuizingen en panelen tegen relatief lage kosten, maar ook voor seriematige verpakkingsoplossingen. Zo worden bijvoorbeeld veel sanitaire modules en machinekappen via vacuümvormen gemaakt, die anders moeilijk betaalbaar te produceren zouden zijn.
Wat is rotatiegieten?
Bij rotatiegieten ook wel rotomoulding genoemd, wordt een nauwkeurig afgemeten hoeveelheid kunststofpoeder in een holle matrijs geplaatst. Deze mal wordt vervolgens in een oven langzaam om twee haakse assen gedraaid. Door de hitte smelt het kunststofpoeder en coat het de binnenwand van de mal gelijkmatig, tot alle wanden bedekt zijn. Zodra het materiaal volledig is uitgesmolten en aangehecht, wordt de mal gekoeld (terwijl hij blijft roteren) zodat het kunststof uithardt. Daarna kan de mal worden geopend en het afgekoelde product worden uitgenomen. Het resultaat van dit proces is een naadloos, hol kunststof product met een gelijkmatige wanddikte over het gehele oppervlak.
Een van de sterke punten van rotatiegieten is dat de matrijskosten relatief laag zijn, waardoor het een ideale keuze is voor kleinere series of startende projecten. In tegenstelling tot spuitgiet- of blaasgietmatrijzen, die vaak duur en complex zijn, kunnen rotatiegietmallen eenvoudiger worden gemaakt. Bovendien biedt de techniek een grote ontwerpvrijheid: complexe vormen, geïntegreerde holle ruimtes of dubbele wanden zijn eenvoudig te realiseren. Omdat het proces geen naden of lassen creëert, ontstaan producten uit één stuk zonder spanningen, wat bijdraagt aan de hoge structurele sterkte. Rotatiegieten is daardoor bijzonder geschikt voor grote en duurzame producten die robuust moeten zijn, zoals opslagtanks, speeltoestellen of andere dikke holle voorwerpen. Ook is het mogelijk om inserts tijdens het proces in te sluiten.
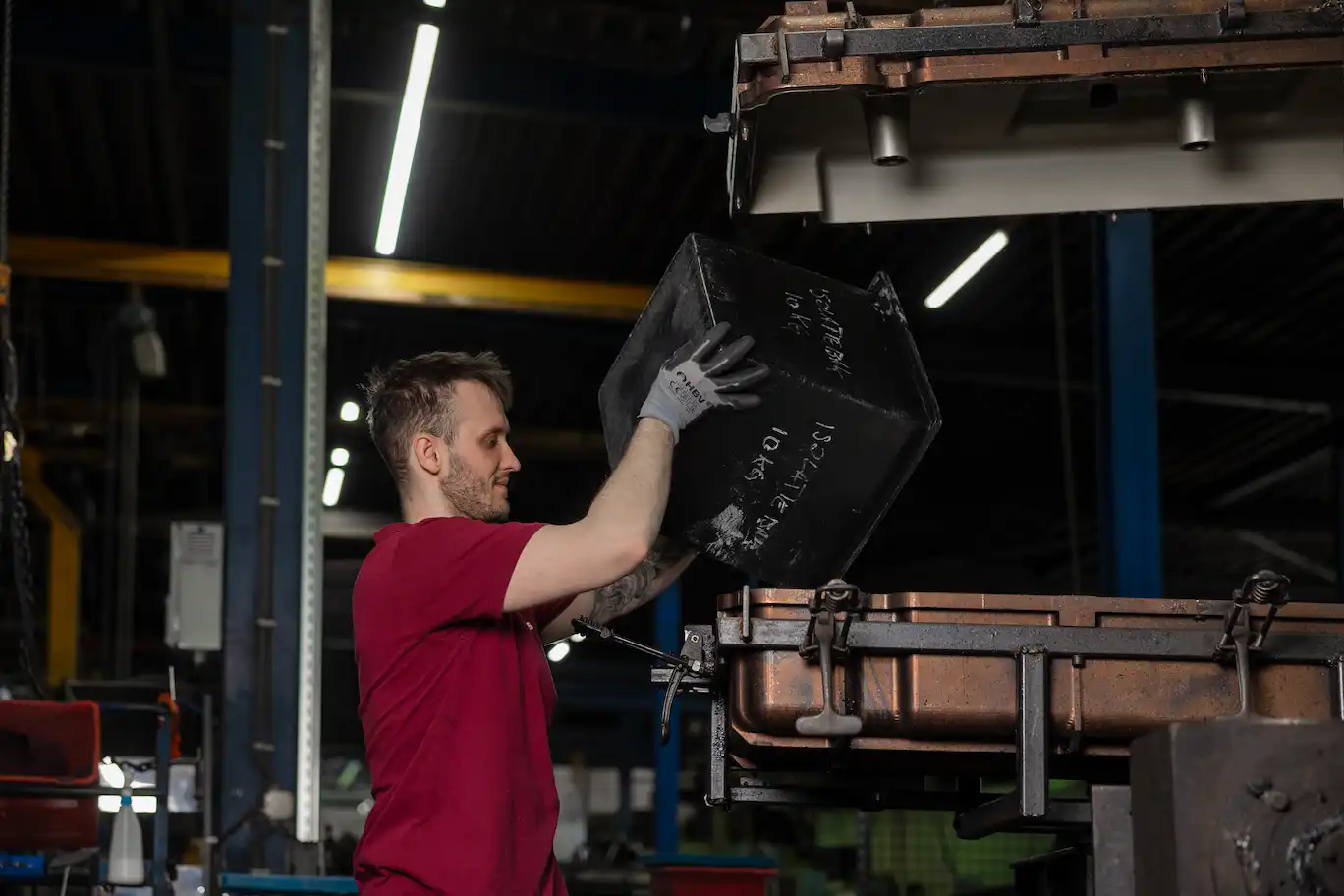
Daarentegen is het rotatiegietproces trager dan vacuümvormen of spuitgieten; elke cyclus duurt langer, omdat het poeder langzaam moet smelten en daarna geleidelijk afkoelt. Dit resulteert in een langere productietijd per stuk. Voor hele grote aantallen kunnen de kosten per product daarom hoger uitvallen vergeleken met snellere technieken. Rotatiegieten is verder minder geschikt voor zeer dunwandige producten; er is een praktische ondergrens aan de wanddikte omdat een zekere materiaalhoeveelheid nodig is om de mal te coaten. Ook is de materiaalkeuze beperkter: in de praktijk wordt vooral polyethyleen (PE) en enkele andere kunststoffen gebruikt die geschikt zijn om tot poeder te malen en gelijkmatig te laten smelten. Hoogwaardige technische kunststoffen die wel vacuümvormbaar zijn (zoals ABS, PC) worden bij rotatiegieten minder toegepast. Ondanks deze beperkingen is rotatiegieten de techniek voor het produceren van holle, stevige producten op een kostenefficiënte manier.
Toepassingen van rotatiegieten:
Rotatiegieten is bij uitstek geschikt voor het produceren van complexe, grote producten die in één stuk worden vervaardigd. Dankzij deze eigenschappen wordt de techniek breed toegepast in sectoren als waterbeheer, landbouw, recreatie, sport, infrastructuur en defensie. Overal waar vormvrijheid, maatwerk, sterkte en duurzaamheid gevraagd worden, biedt rotatiegieten een flexibele en efficiënte oplossing.
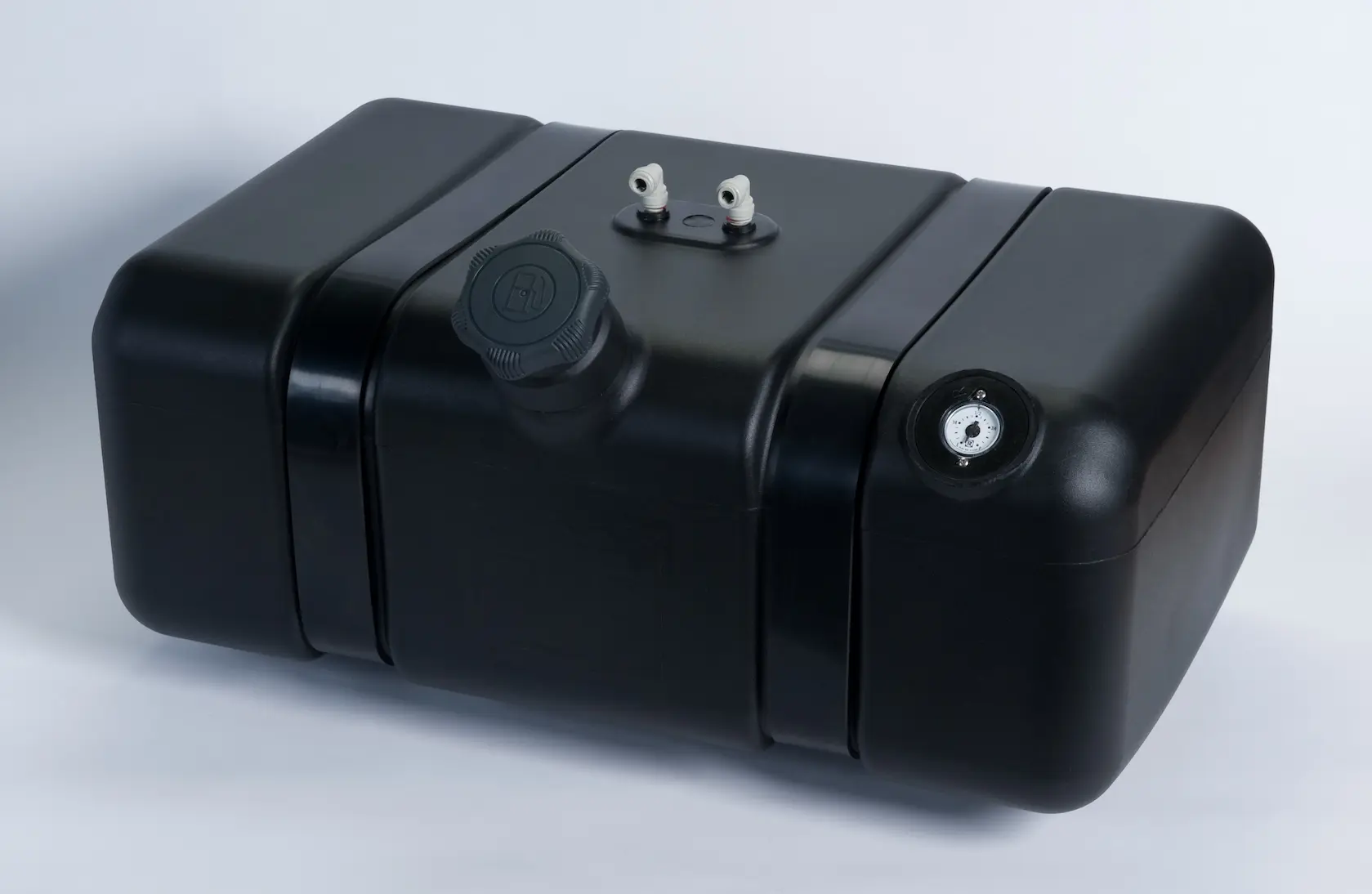
Welke techniek kies je?
De keuze tussen vacuümvormen en rotatiegieten hangt af van diverse factoren, zoals het gewenste productievolume, de complexiteit van het ontwerp en de kosten. Hieronder zetten we de overwegingen op een rij.
Vacuümvormen
Vacuümvormen is met name geschikt voor de productie van relatief lichte of dunwandige onderdelen in middelgrote tot grote aantallen. Door de snellere cyclustijden en de mogelijkheid om met verschillende kunststoffen te werken, biedt deze techniek een kostenefficiënte oplossing voor serieproductie. Bovendien zijn de instapkosten laag, wat aantrekkelijk is voor kleine series en prototyping. Wel moeten de ontwerpen relatief eenvoudig zijn (geen volledig gesloten holle vormen) en houd je rekening met wat variatie in wanddikte. Voor toepassingen waar gewichtsbesparing en hoge aantallen centraal staan denk aan productverpakkingen, kunststof panelen of interieurdelen kan vacuümvormen de beste keuze zijn.
Rotatiegieten
Rotatiegieten is daarentegen ideaal voor producten met een complex ontwerp of grotere fysieke afmetingen, waarbij een gelijkmatige wanddikte en hoge structurele sterkte vereist zijn. De lage matrijskosten maken deze techniek interessant voor kleinere tot middelgrote series, terwijl de naadloze constructie bijdraagt aan een uitstekende duurzaamheid. Bovendien kunnen met rotatiegieten zeer grote producten worden vervaardigd, zoals opslagtanks of speeltoestellen, die met vacuümvormen niet of nauwelijks uit één stuk te maken zijn. Wanneer een product robuust moet zijn en bijvoorbeeld dubbele wanden of holle ruimtes bevat, is rotatiegieten vaak de aangewezen methode. Houd er rekening mee dat de cyclustijd langer is, waardoor bij hele grote aantallen de stukprijs hoger kan uitvallen dan bij vacuümvormen.
Eigenschap | Rotatiegieten | Vacuümvormen |
---|---|---|
Productievolume | Ideaal voor kleine tot middelgrote oplages (circa 400 – 50.000 stuks). | Geschikt voor kleine én grote series, van enkele prototypes tot tienduizenden stuks (afhankelijk van producttype). |
Kosten per product | Hoger door langere productietijd per stuk. | Lager bij hogere aantallen, dankzij kortere cyclustijden. |
Matrijskosten | Relatief laag | Zeer laag (lage instapkosten voor mallen). |
Wanddikte | Dik met een overwegend gelijkmatige verdeling, afhankelijk van vorm en ontwerp. | Dunner, moeilijk overal gelijkmatig. |
Ontwerpvrijheid | Zeer flexibel, geschikt voor complexe, holle ontwerpen. | Beperkt tot vrij eenvoudige, ondiepe vormen (enkelzijdige details). |
Mechanische sterkte | Naadloos product, zeer sterk en duurzaam. | Niet naadloos; open randen en variabele dikte kunnen zwakke punten geven. |
Een passende oplossing voor elk project
Benieuwd welke productietechniek het beste past bij jouw project? Bij Pentas denken we graag met je mee! Neem contact met ons op en ontdek hoe we jouw product idee tot leven kunnen brengen. We bespreken graag de mogelijkheden en vinden samen de perfecte oplossing.