Rotational moulding vs. vacuum forming
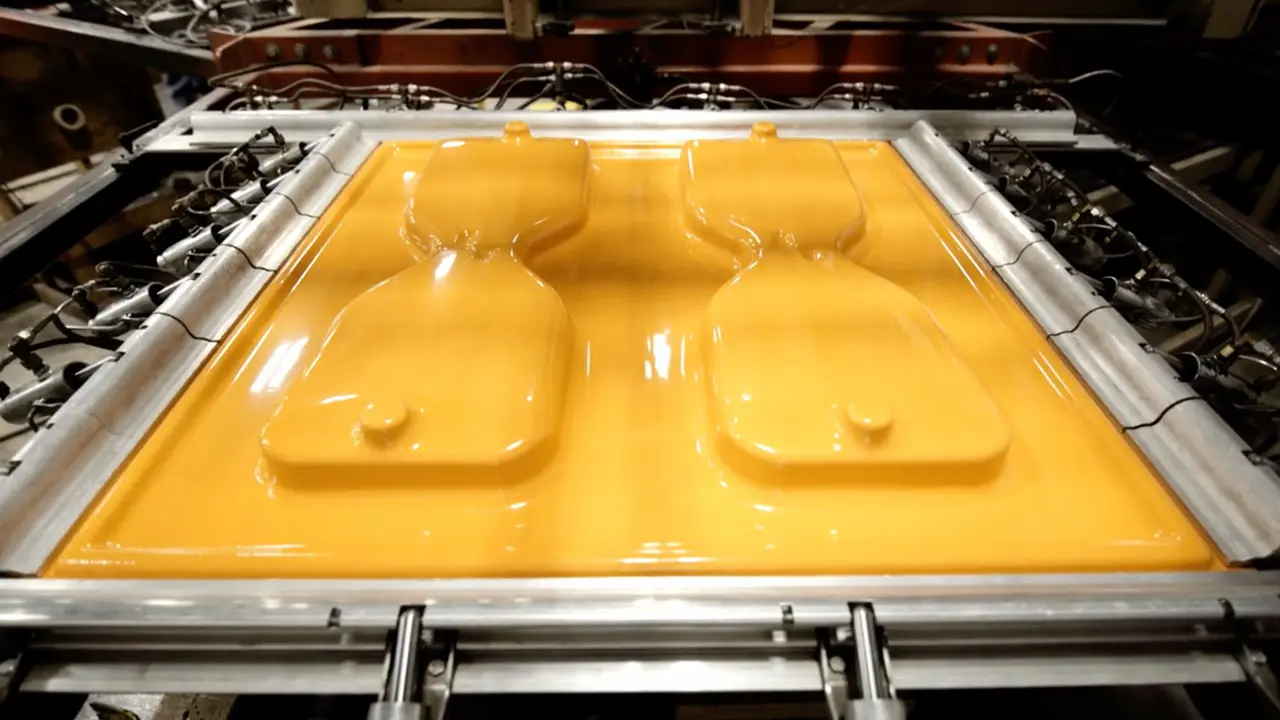
Do you want to have a plastic product manufactured and are you hesitating between rotational moulding and vacuum forming? Both production techniques have their own advantages, depending on the design, batch size and desired properties. Pentas specialises in rotational moulding, but we understand that not every product is suitable for this. Vacuum forming is an alternative production method with different characteristics and advantages. In this article, we compare both techniques so you can better determine which method is most suitable for your product.
Table of contents
What is vacuum forming?
Vacuum forming is a production method in which a plastic sheet (thermoplastic) is heated until it becomes malleable and then drawn over a mould using vacuum. The material takes the shape of the mould. Once cooled, the plastic retains this shape, creating the desired part. This technique is applied to a wide range of products, from blister packaging to machine housings and interior panels.
The vacuum forming process involves four steps:
Heating the plastic sheet: A flat thermoplastic sheet (e.g. ABS or PETG) is clamped and gradually heated until it becomes soft and formable.
Forming over the mould: The warm sheet is placed over the mould. The air between the sheet and the mould is then evacuated so that the plastic sheet is pulled tightly against the contours of the mould, precisely following its shape.
Cooling: While maintaining the vacuum, the formed plastic cools down. The sheet hardens into its new shape and retains it after cooling. Cooling fans can be used to speed up the process.
Removing and finishing: The hardened product is removed from the mould. Excess material, such as edges or the sheet surrounding the product, is cut or milled off. Any post-processing (e.g. drilling holes or cutting openings) takes place at this stage to make the part ready for use.
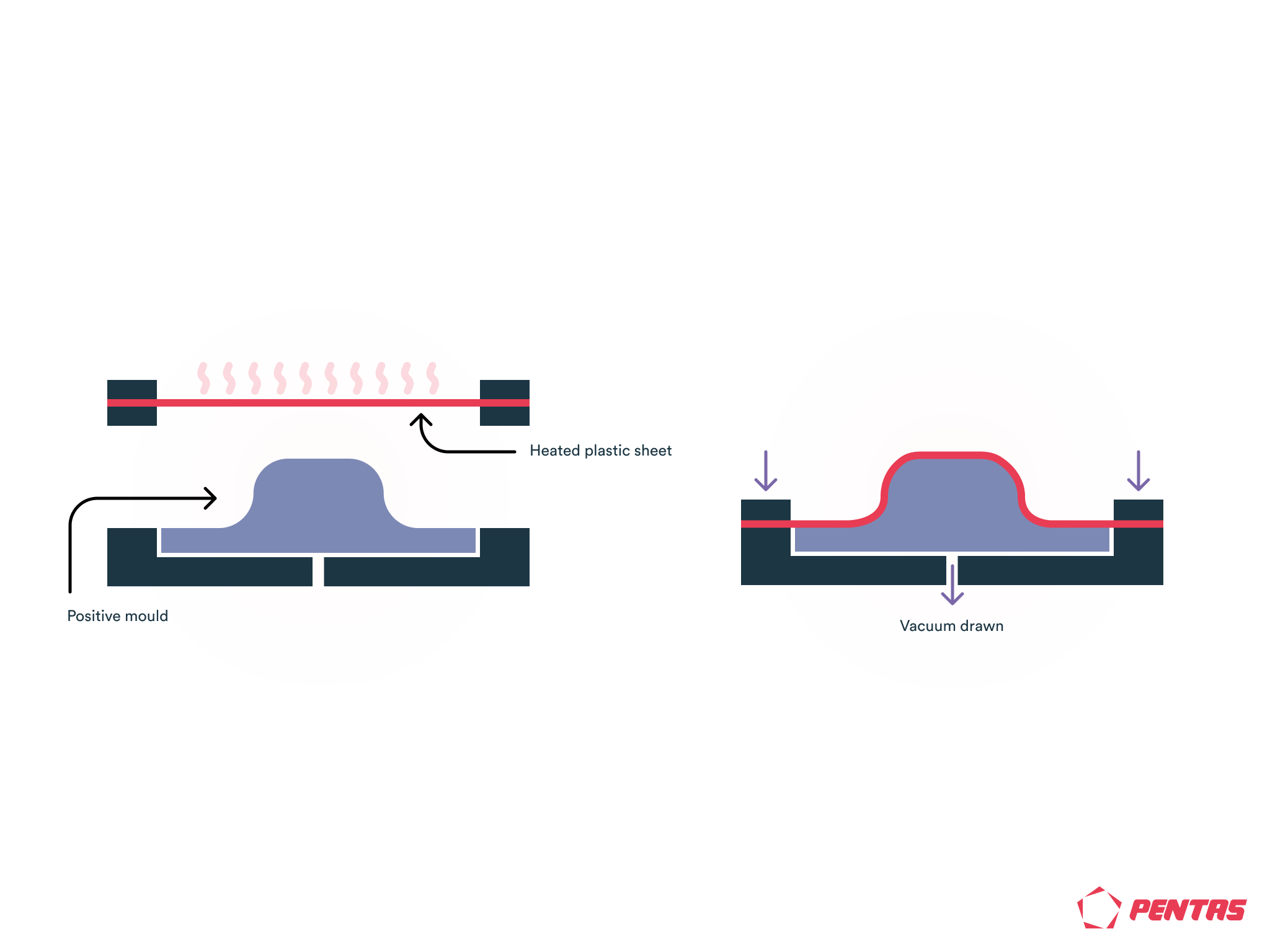
One of the biggest advantages of vacuum forming is the low investment threshold for new products. The mould costs are low, especially compared to injection moulding or blow moulding. This makes the technique attractive for small series, prototypes and customised products. In addition, relatively large plastic products can be made using vacuum forming (depending on the machine, often up to several metres). A wide range of materials can be used: many thermoplastics such as ABS, polystyrene, PET, PVC and polycarbonate are suitable. The cycle times are also shorter than, for example, rotational moulding, allowing lower cost per unit for series production. Vacuum forming is therefore a cost-effective method for both small batches and larger series.
However, there are limitations. The design freedom is more limited than with rotational moulding or injection moulding; complex or very deep shapes with undercuts are difficult to achieve with vacuum forming. As the material stretches during forming, variations in wall thickness may occur (thinner areas where the material is heavily stretched). Furthermore, relatively much excess material is generated around the product, which must be trimmed after forming. Finally, vacuum-formed products cannot have integral details such as threads or complex ribs formed; such features must be added later (e.g. by milling or assembly). Despite these limitations, vacuum forming is a very versatile technique for many applications where a relatively simple shape suffices.
Applications of vacuum forming:
Vacuum forming is especially suitable for producing larger plastic housings and panels at relatively low cost, but also for serial packaging solutions. For example, many sanitary modules and machine covers are made by vacuum forming that would otherwise be difficult and costly to produce.
What is rotational moulding?
In rotational moulding, also called rotomoulding, a precisely measured amount of plastic powder is placed into a hollow mould. This mould is then slowly rotated around two perpendicular axes inside an oven. The heat melts the plastic powder, coating the inside wall of the mould evenly until all surfaces are covered. Once the material is fully melted and bonded, the mould is cooled (while still rotating) so that the plastic solidifies. The mould is then opened and the cooled product is removed. The result of this process is a seamless, hollow plastic product with an even wall thickness throughout.
One of the strengths of rotational moulding is that mould costs are relatively low, making it an ideal choice for smaller series or start-up projects. Unlike injection or blow moulds, which are often expensive and complex, rotational moulding moulds are simpler to make. Moreover, the technique offers great design freedom: complex shapes, integrated hollow spaces or double walls are easy to realise. Since the process creates no seams or welds, products are formed in one piece without stress, contributing to high structural strength. Rotational moulding is therefore particularly suitable for large and durable products that need to be robust, such as storage tanks, playground equipment or other thick-walled hollow objects. It is also possible to embed inserts during the process.
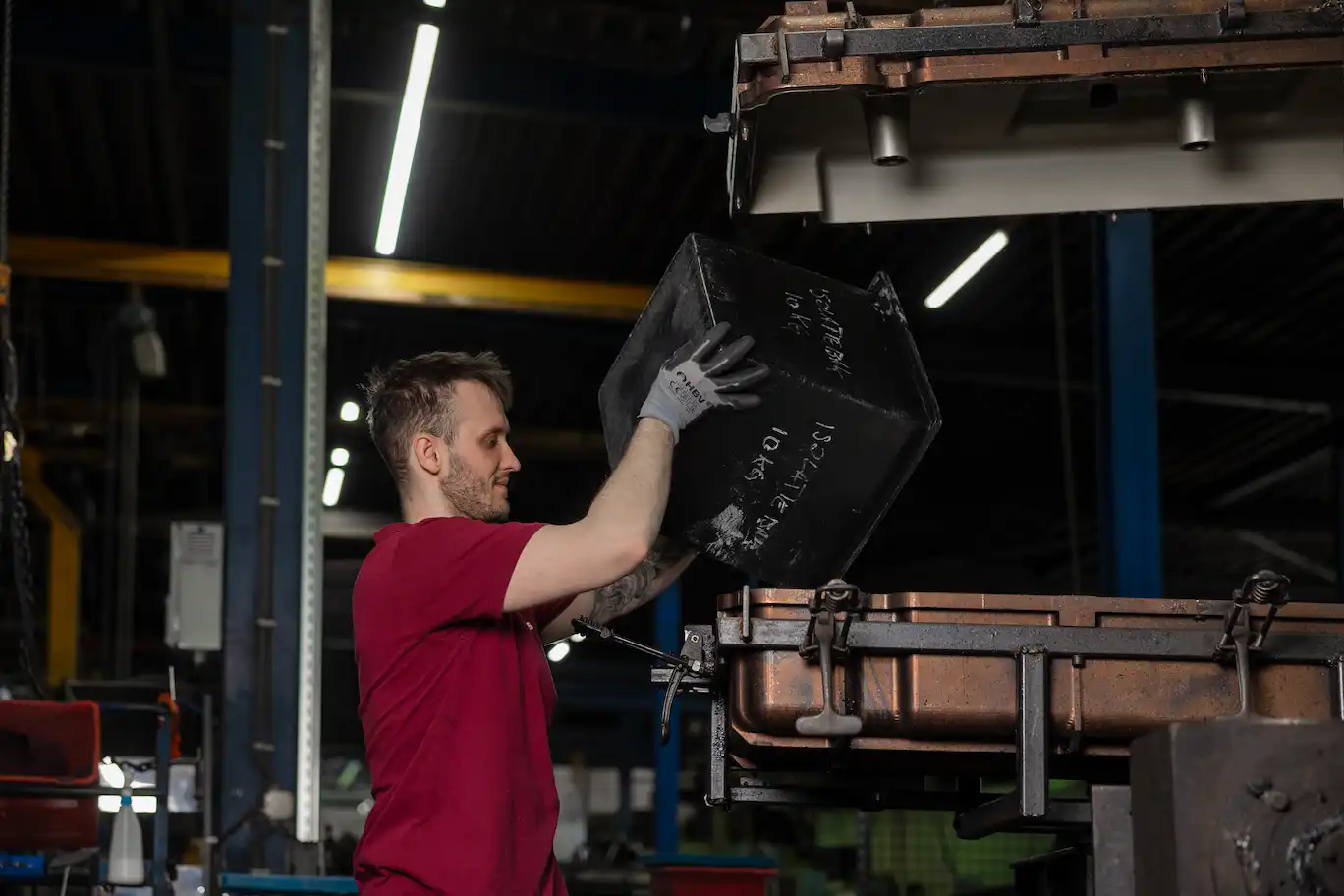
On the other hand, the rotational moulding process is slower than vacuum forming or injection moulding; each cycle takes longer, as the powder must slowly melt and then gradually cool. This results in a longer production time per unit. For very large quantities, the cost per product may therefore be higher compared to faster techniques. Rotational moulding is also less suitable for very thin-walled products; there is a practical lower limit to wall thickness because a certain amount of material is needed to coat the mould. The material choice is also more limited: in practice, mainly polyethylene (PE) and a few other plastics that can be powdered and evenly melted are used. High-grade engineering plastics that are vacuum formable (such as ABS, PC) are less commonly used in rotational moulding. Despite these limitations, rotational moulding is the technique for producing hollow, sturdy products in a cost-efficient manner.
Applications of rotational moulding:
Rotational moulding is ideally suited for producing complex, large products made in one piece. Thanks to these properties, the technique is widely used in sectors such as water management, agriculture, recreation, sports, infrastructure and defence. Wherever design freedom, customisation, strength and durability are required, rotational moulding offers a flexible and efficient solution.
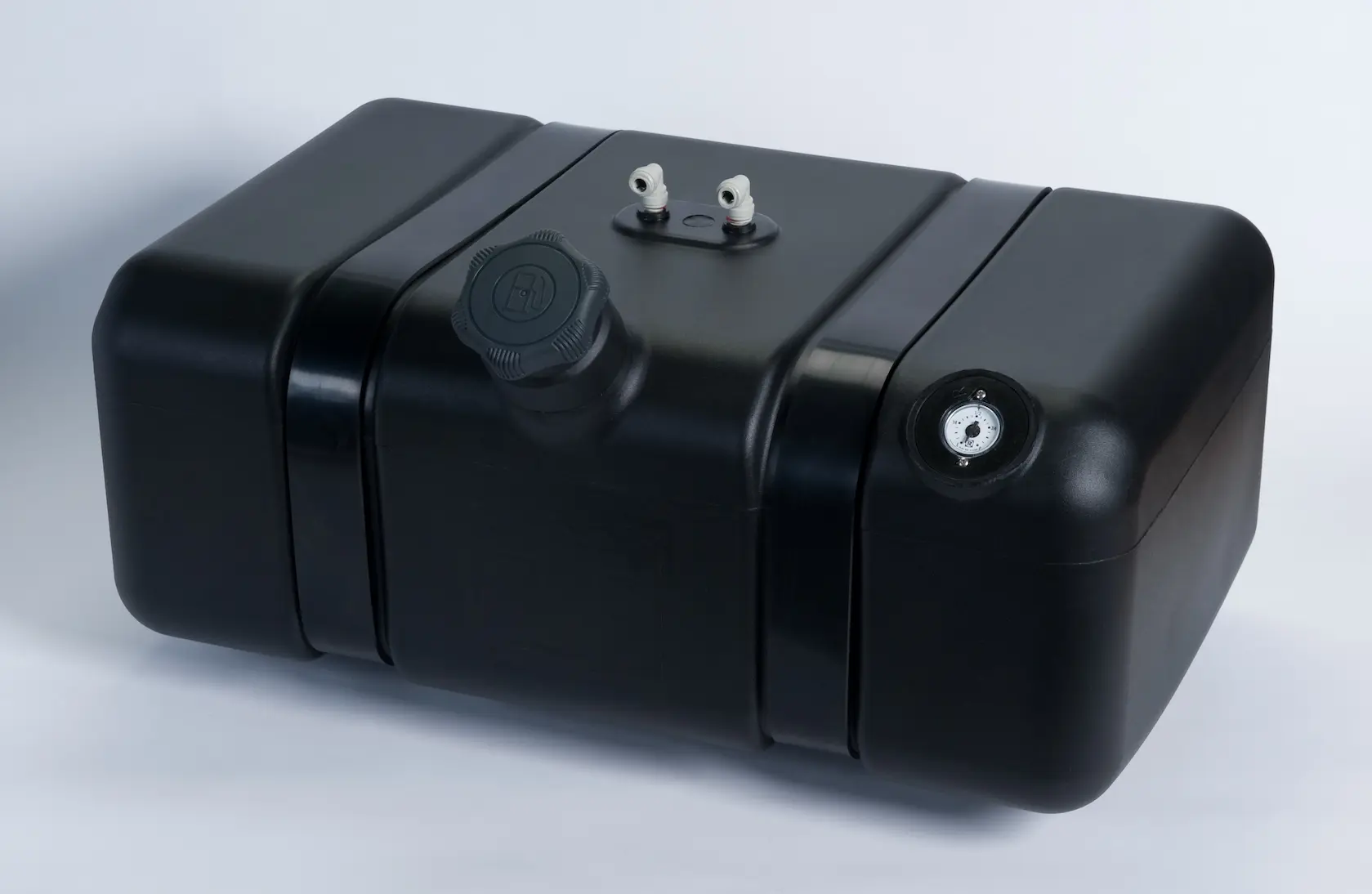
Which technique should you choose?
The choice between vacuum forming and rotational moulding depends on various factors, such as the desired production volume, the complexity of the design, and costs. Below, we list the considerations.
Vacuum forming
Vacuum forming is particularly suitable for producing relatively lightweight or thin-walled parts in medium to large quantities. Thanks to faster cycle times and the ability to work with different plastics, this technique offers a cost-efficient solution for series production. Moreover, the entry costs are low, making it attractive for small series and prototyping. However, the designs need to be relatively simple (no fully enclosed hollow shapes), and some variation in wall thickness should be considered. For applications where weight reduction and high volumes are central—think of product packaging, plastic panels, or interior parts—vacuum forming may be the best choice.
Rotational moulding
Rotational moulding, on the other hand, is ideal for products with a complex design or larger physical dimensions, where uniform wall thickness and high structural strength are required. The low mould costs make this technique attractive for small to medium series, while the seamless construction contributes to excellent durability. Additionally, rotational moulding can be used to produce very large products, such as storage tanks or playground equipment, which are difficult or impossible to manufacture in one piece using vacuum forming. When a product needs to be robust and includes, for example, double walls or hollow spaces, rotational moulding is often the preferred method. Keep in mind that the cycle time is longer, which may result in a higher unit price for very large quantities compared to vacuum forming.
Property | Rotational moulding | Vacuum forming |
---|---|---|
Production volume | Ideal for small to medium runs (approx. 400 – 50,000 units). | Suitable for small and large series, from a few prototypes to tens of thousands of units (depending on product type). |
Cost per product | Higher due to longer production time | Lower for higher quantities, thanks to shorter cycle times. |
Mould costs | Relatively low | Very low (low entry costs for moulds). |
Wall thickness | Thick with predominantly even distribution, depending on shape and design. | Thinner, difficult to keep uniform everywhere. |
Design freedom | Very flexible, suitable for complex, hollow designs. | Limited to fairly simple, shallow shapes (single-sided details). |
Mechanical strength | Seamless, strong, and durable | Not seamless; open edges and variable thickness can create weak points. |
A suitable solution for every project
Curious which production technique best suits your project? At Pentas we are happy to think along with you! Contact us and discover how we can bring your product idea to life. We are happy to discuss the possibilities and find the perfect solution together.