Rotationsguss vs. Vakuumformen
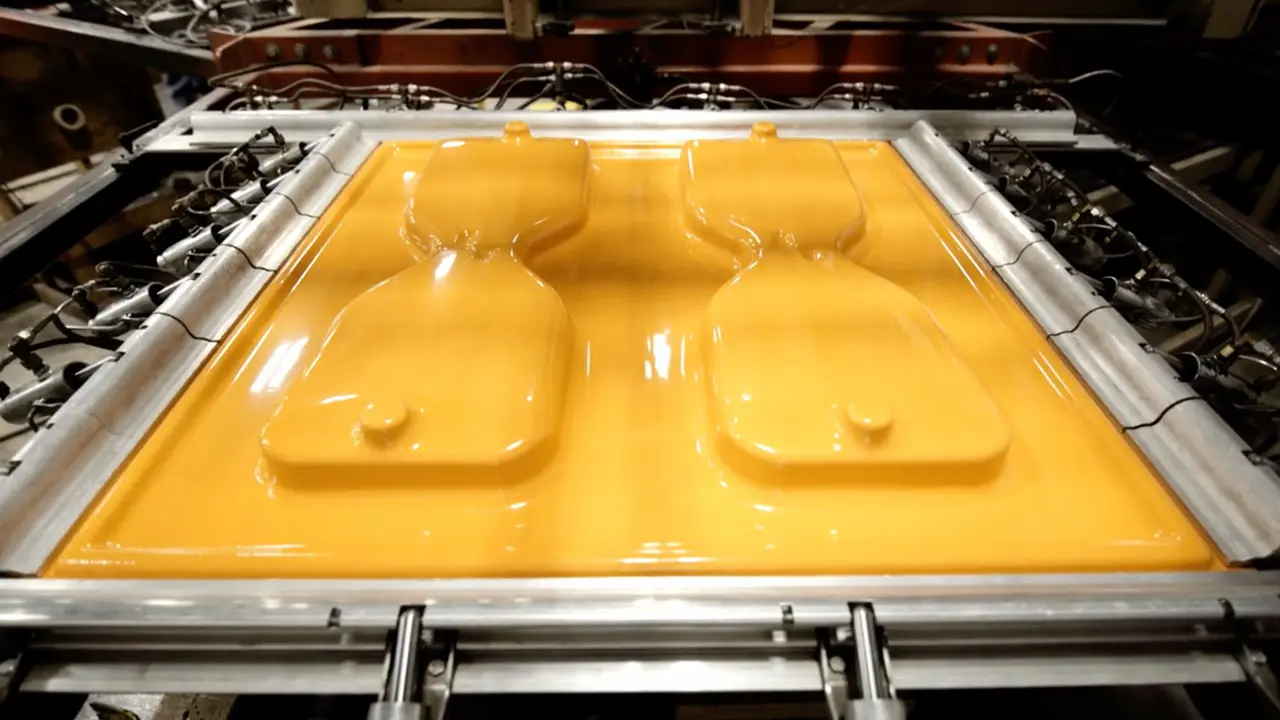
Möchten Sie ein Kunststoffprodukt herstellen lassen und schwanken zwischen Rotationsguss und Vakuumformen? Beide Fertigungsverfahren haben ihre eigenen Vorteile, abhängig von Design, Stückzahl und den gewünschten Eigenschaften. Pentas ist Spezialist für Rotationsguss, aber wir verstehen, dass sich nicht jedes Produkt dafür eignet. Vakuumformen ist ein alternatives Fertigungsverfahren mit anderen Merkmalen und Vorteilen. In diesem Artikel vergleichen wir beide Techniken, damit Sie besser entscheiden können, welche Methode für Ihr Produkt am besten geeignet ist.
Table of contents
Was ist Vakuumformen?
Beim Vakuumformen wird eine Kunststoffplatte (Thermoplast) erhitzt, bis sie verformbar ist, und anschließend mithilfe von Unterdruck über eine Form gezogen. Dadurch nimmt das Material die Form des Werkzeugs an. Nach dem Abkühlen behält der Kunststoff diese Form, wodurch das gewünschte Bauteil entsteht. Diese Technik wird für unterschiedlichste Produkte eingesetzt, von Blisterverpackungen bis zu Maschinengehäusen und Interieurpaneelen.
Der Vakuumformprozess erfolgt in vier Schritten:
Erwärmen der Kunststoffplatte: Eine flache thermoplastische Kunststoffplatte (z. B. ABS oder PETG) wird eingespannt und schrittweise erhitzt, bis sie weich und formbar ist.
Formen über die Matrize: Die warme Platte wird über die Form gelegt. Anschließend wird die Luft zwischen Platte und Form abgesaugt, sodass die Kunststoffplatte eng an die Konturen der Form gezogen wird und diese exakt nachbildet.
Abkühlen: Während der Unterdruck aufrechterhalten wird, kühlt der geformte Kunststoff ab. Die Platte härtet in der neuen Form aus und behält diese nach dem Abkühlen. Kühlventilatoren können den Prozess beschleunigen.
Entnahme und Nachbearbeitung: Das ausgehärtete Produkt wird aus der Form genommen. Überstehendes Material wie Ränder oder der restliche Plattenbereich wird abgeschnitten oder gefräst. In dieser Phase erfolgen auch eventuelle Nachbearbeitungen (z. B. Bohren von Löchern oder Ausschneiden), um das Bauteil einsatzbereit zu machen.
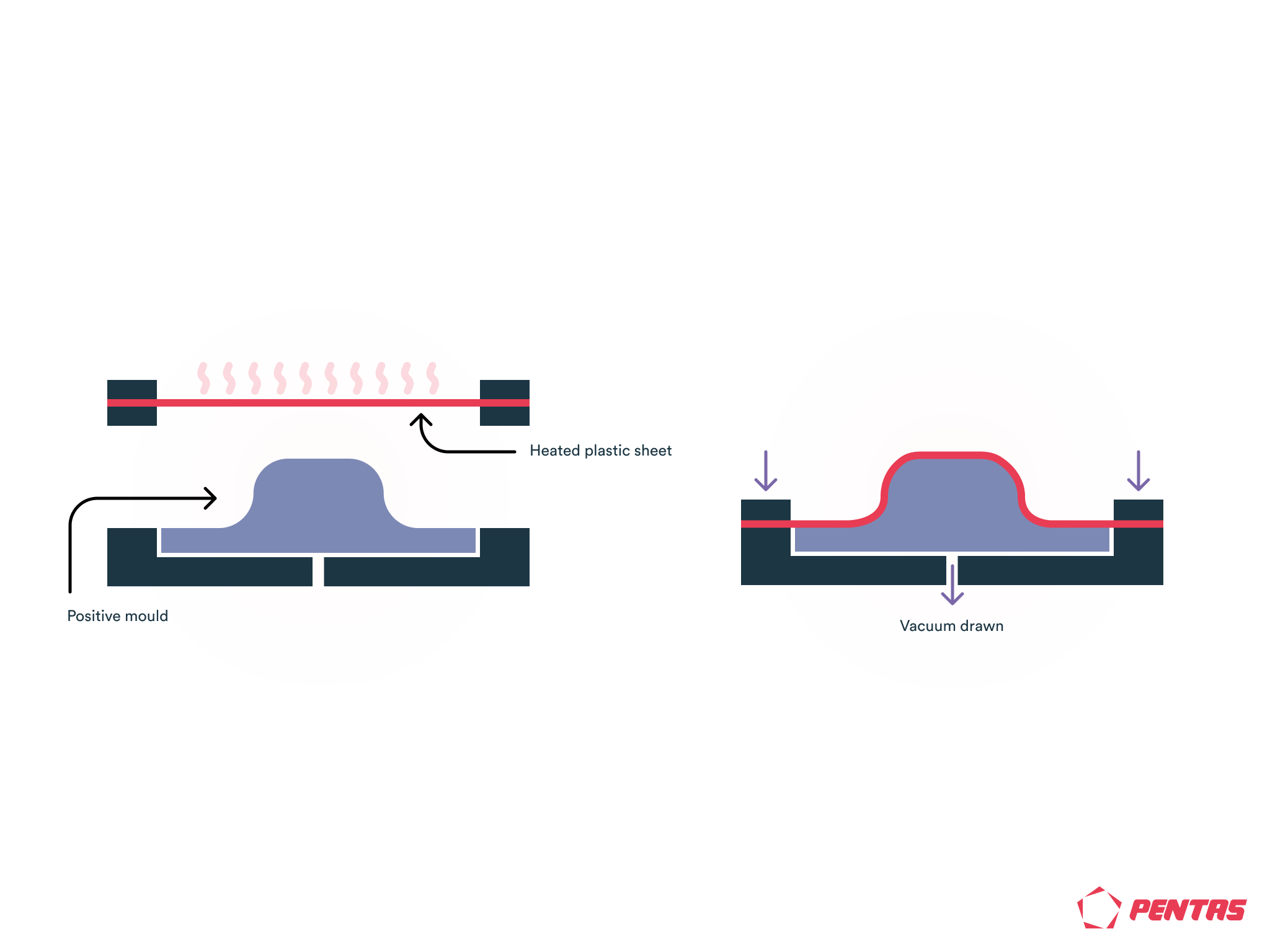
Einer der größten Vorteile des Vakuumformens sind die niedrigen Investitionskosten für neue Produkte. Die Werkzeugkosten sind gering, insbesondere im Vergleich zum Spritz- oder Blasformen. Dadurch eignet sich das Verfahren gut für kleine Serien, Prototypen und kundenspezifische Produkte. Zudem können mit Vakuumformen relativ große Kunststoffprodukte gefertigt werden (je nach Maschine oft bis zu mehreren Metern). Es steht eine breite Materialauswahl zur Verfügung: viele Thermoplaste wie ABS, Polystyrol, PET, PVC und Polycarbonat eignen sich. Auch die Zykluszeiten sind kürzer als beispielsweise beim Rotationsguss, wodurch bei Serienfertigung die Stückkosten niedrig gehalten werden können. Vakuumformen ist somit eine kosteneffiziente Methode sowohl für Klein- als auch Großserien.
Dennoch gibt es Einschränkungen. Die Gestaltungsfreiheit ist geringer als beim Rotationsguss oder Spritzguss; komplexe oder sehr tiefe Formen mit Hinterschneidungen lassen sich mit Vakuumformen nur schwer umsetzen. Da das Material beim Formen gedehnt wird, können Wandstärkenunterschiede auftreten (dünnere Bereiche an stark gedehnten Stellen). Zudem entsteht relativ viel Verschnittmaterial, das nach dem Formen entfernt werden muss. Schließlich können beim Vakuumformen keine integralen Details wie Gewinde oder komplexe Rippen direkt mitgeformt werden; solche Funktionen müssen später hinzugefügt werden (z. B. durch Fräsen oder Montage). Trotz dieser Einschränkungen ist Vakuumformen eine sehr vielseitige Technik für zahlreiche Anwendungen, bei denen eine relativ einfache Form genügt.
Anwendungsbereiche des Vakuumformens:
Vakuumformen eignet sich besonders für die Herstellung größerer Kunststoffgehäuse und -platten zu relativ geringen Kosten, aber auch für serielle Verpackungslösungen. So werden z. B. viele Sanitärmodule und Maschinenverkleidungen per Vakuumformen hergestellt, die auf anderem Wege schwer und teuer zu produzieren wären.
Was ist Rotationsguss?
Beim Rotationsguss wird eine genau abgemessene Menge Kunststoffpulver in eine hohle Form gegeben. Diese Form wird anschließend in einem Ofen langsam um zwei senkrechte Achsen gedreht. Durch die Hitze schmilzt das Kunststoffpulver und beschichtet gleichmäßig die Innenwände der Form, bis alle Bereiche bedeckt sind. Sobald das Material vollständig geschmolzen und angehaftet ist, wird die Form (weiter rotierend) abgekühlt, damit der Kunststoff aushärtet. Danach kann die Form geöffnet und das abgekühlte Produkt entnommen werden. Das Ergebnis ist ein nahtloses, hohles Kunststoffprodukt mit gleichmäßiger Wandstärke über die gesamte Oberfläche.
Ein großer Vorteil des Rotationsgusses sind die vergleichsweise niedrigen Werkzeugkosten, wodurch es ideal für kleinere Serien oder Startprojekte geeignet ist. Im Gegensatz zu Spritzguss- oder Blasformen, die oft teuer und komplex sind, lassen sich Rotationsgussformen einfacher herstellen. Zudem bietet das Verfahren große Gestaltungsfreiheit: komplexe Formen, integrierte Hohlräume oder Doppelwände sind problemlos realisierbar. Da beim Prozess keine Nähte oder Schweißstellen entstehen, werden die Produkte spannungsfrei aus einem Stück gefertigt, was die hohe strukturelle Festigkeit unterstützt. Rotationsguss eignet sich daher besonders für große und langlebige Produkte, die robust sein müssen, wie Tanks, Spielgeräte oder andere dickwandige Hohlkörper. Auch das Einlegen von Einsätzen während des Prozesses ist möglich.
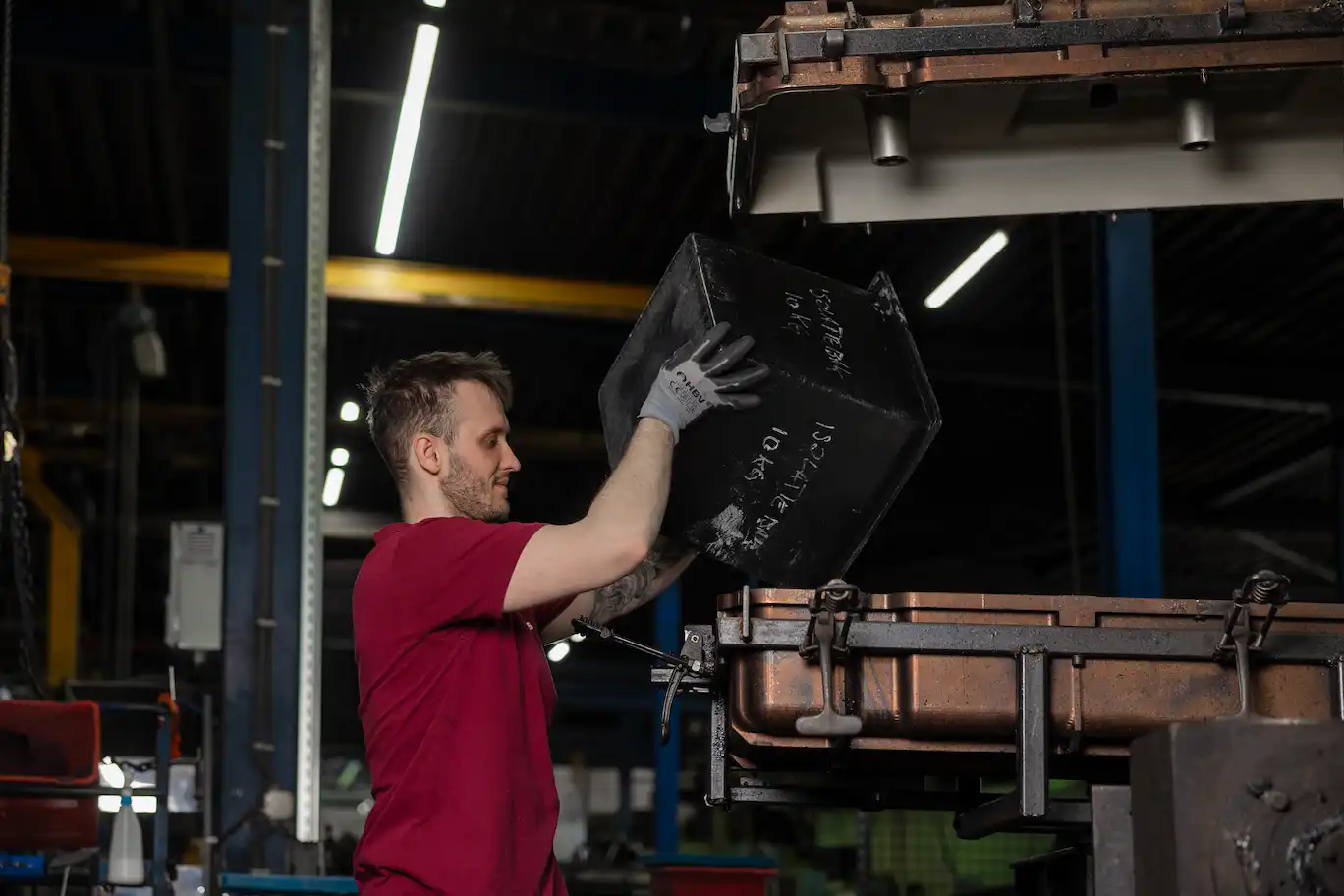
Allerdings ist der Rotationsguss langsamer als Vakuumformen oder Spritzguss; jeder Zyklus dauert länger, da das Pulver langsam schmelzen und danach behutsam abkühlen muss. Dies führt zu längeren Produktionszeiten pro Stück. Bei sehr großen Stückzahlen können die Kosten pro Produkt daher höher ausfallen als bei schnelleren Verfahren. Rotationsguss eignet sich zudem weniger für sehr dünnwandige Produkte; es gibt eine praktische Mindestwandstärke, da eine gewisse Materialmenge erforderlich ist, um die Form zu beschichten. Auch die Materialauswahl ist begrenzter: in der Praxis werden hauptsächlich Polyethylen (PE) und einige andere Kunststoffe verwendet, die pulverisiert und gleichmäßig geschmolzen werden können. Hochwertige technische Kunststoffe, die vakuumformbar sind (wie ABS, PC), werden beim Rotationsguss kaum eingesetzt. Trotz dieser Einschränkungen ist Rotationsguss die Technik zur effizienten Herstellung von hohlen, stabilen Produkten.
Anwendungsbereiche des Rotationsgusses:
Rotationsguss eignet sich hervorragend für die Herstellung komplexer, großer Produkte aus einem Stück. Dank dieser Eigenschaften wird die Technik breit in Bereichen wie Wasserwirtschaft, Landwirtschaft, Freizeit, Sport, Infrastruktur und Verteidigung eingesetzt. Überall dort, wo Gestaltungsfreiheit, Individualisierung, Stabilität und Langlebigkeit gefragt sind, bietet Rotationsguss eine flexible und effiziente Lösung.
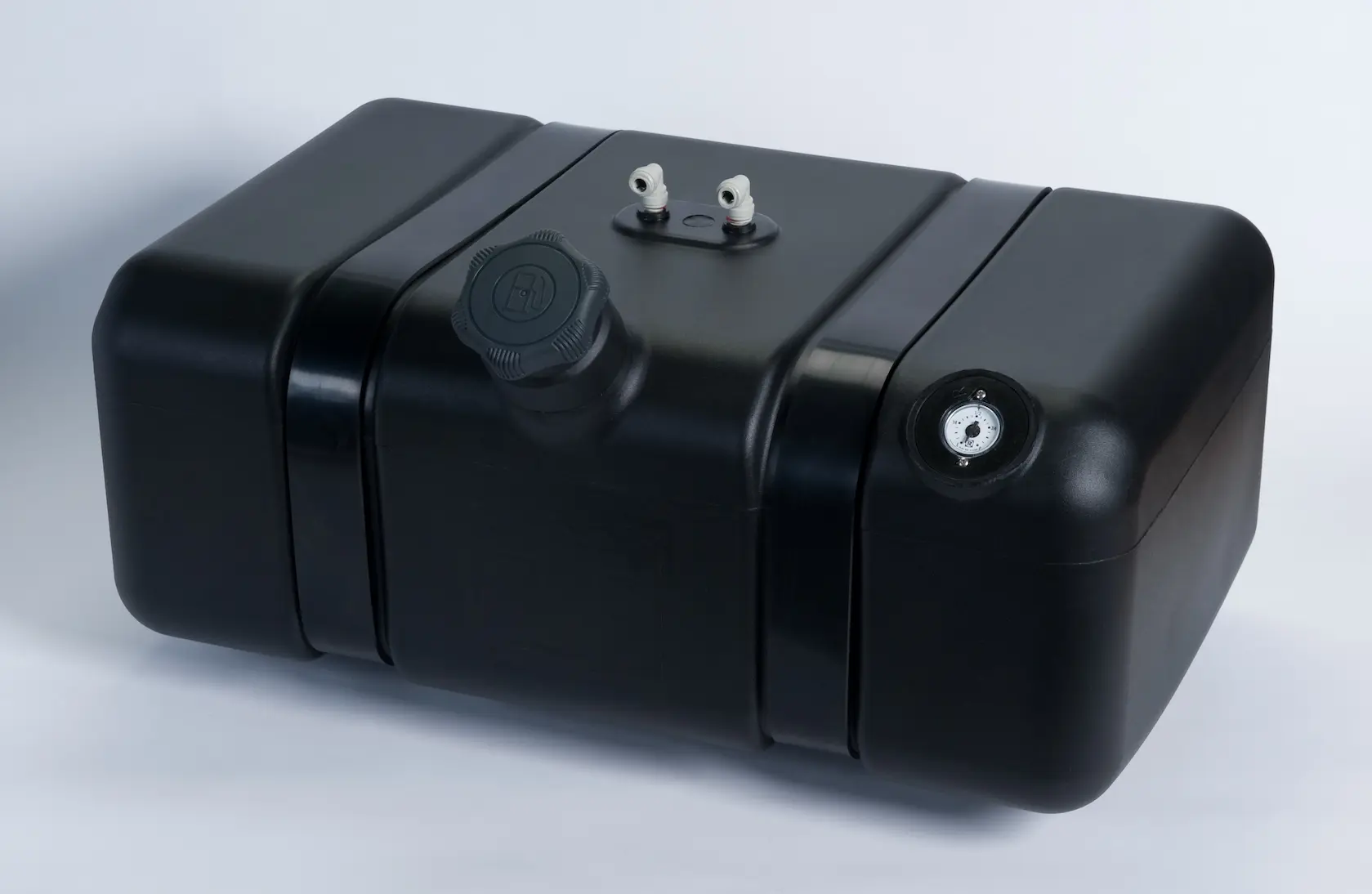
Welche Technik wählen Sie?
Die Wahl zwischen Vakuumformen und Rotationsguss hängt von verschiedenen Faktoren ab, wie dem gewünschten Produktionsvolumen, der Komplexität des Designs und den Kosten. Nachfolgend sind die Überlegungen aufgeführt.
Vakuumformen
Vakuumformen eignet sich besonders für die Herstellung von relativ leichten oder dünnwandigen Bauteilen in mittleren bis großen Stückzahlen. Dank der schnelleren Zykluszeiten und der Möglichkeit, mit verschiedenen Kunststoffen zu arbeiten, bietet diese Technik eine kosteneffiziente Lösung für die Serienproduktion. Zudem sind die Einstiegskosten niedrig, was sie für Kleinserien und Prototyping attraktiv macht. Die Designs müssen jedoch relativ einfach sein (keine vollständig geschlossenen Hohlformen), und es ist mit gewissen Schwankungen in der Wandstärke zu rechnen. Für Anwendungen, bei denen Gewichtseinsparung und hohe Stückzahlen im Vordergrund stehen – zum Beispiel Produktverpackungen, Kunststoffpaneele oder Interieurteile – kann Vakuumformen die beste Wahl sein.
Rotationsguss
Rotationsguss hingegen ist ideal für Produkte mit komplexem Design oder größeren physischen Abmessungen, bei denen eine gleichmäßige Wandstärke und hohe strukturelle Festigkeit erforderlich sind. Die niedrigen Werkzeugkosten machen diese Technik für kleine bis mittlere Serien interessant, während die nahtlose Konstruktion zu einer hervorragenden Haltbarkeit beiträgt. Außerdem können mit Rotationsguss sehr große Produkte hergestellt werden, wie zum Beispiel Lagertanks oder Spielgeräte, die mit Vakuumformen kaum oder gar nicht in einem Stück produziert werden können. Wenn ein Produkt robust sein muss und beispielsweise Doppelwände oder Hohlräume enthält, ist Rotationsguss oft die bevorzugte Methode. Es ist jedoch zu beachten, dass die Zykluszeit länger ist, wodurch bei sehr großen Stückzahlen der Stückpreis höher ausfallen kann als beim Vakuumformen.
Eigenschaft | Rotationsguss | Blasformen |
---|---|---|
Produktionsvolumen | Ideal für kleine bis mittlere Serien (10 - 5.000 Stück), aber auch bis zu 50.000 Stück möglich | Geeignet für große Serien (>10.000 Stück) |
Kosten pro Produkt | Höher aufgrund längerer Produktionszeit | Niedrig bei hohen Stückzahlen |
Werkzeugkosten | Relativ niedrig | Hoch |
Wandstärke | Dick und gleichmäßig | Dünn, schwer zu variieren |
Designfreiheit | Sehr flexibel, geeignet für komplexe Formen | Eingeschränkt, vor allem einfache Formen |
Mechanische Festigkeit | Nahtlos, stabil und langlebig | Kann Nähte und Schwachstellen enthalten |
Die passende Lösung für jedes Projekt
Neugierig, welche Produktionstechnik am besten zu Ihrem Projekt passt? Wir bei Pentas beraten Sie gerne! Nehmen Sie Kontakt mit uns auf und entdecken Sie, wie wir Ihre Produktidee realisieren können. Gemeinsam finden wir die perfekte Lösung.