The art of mould making
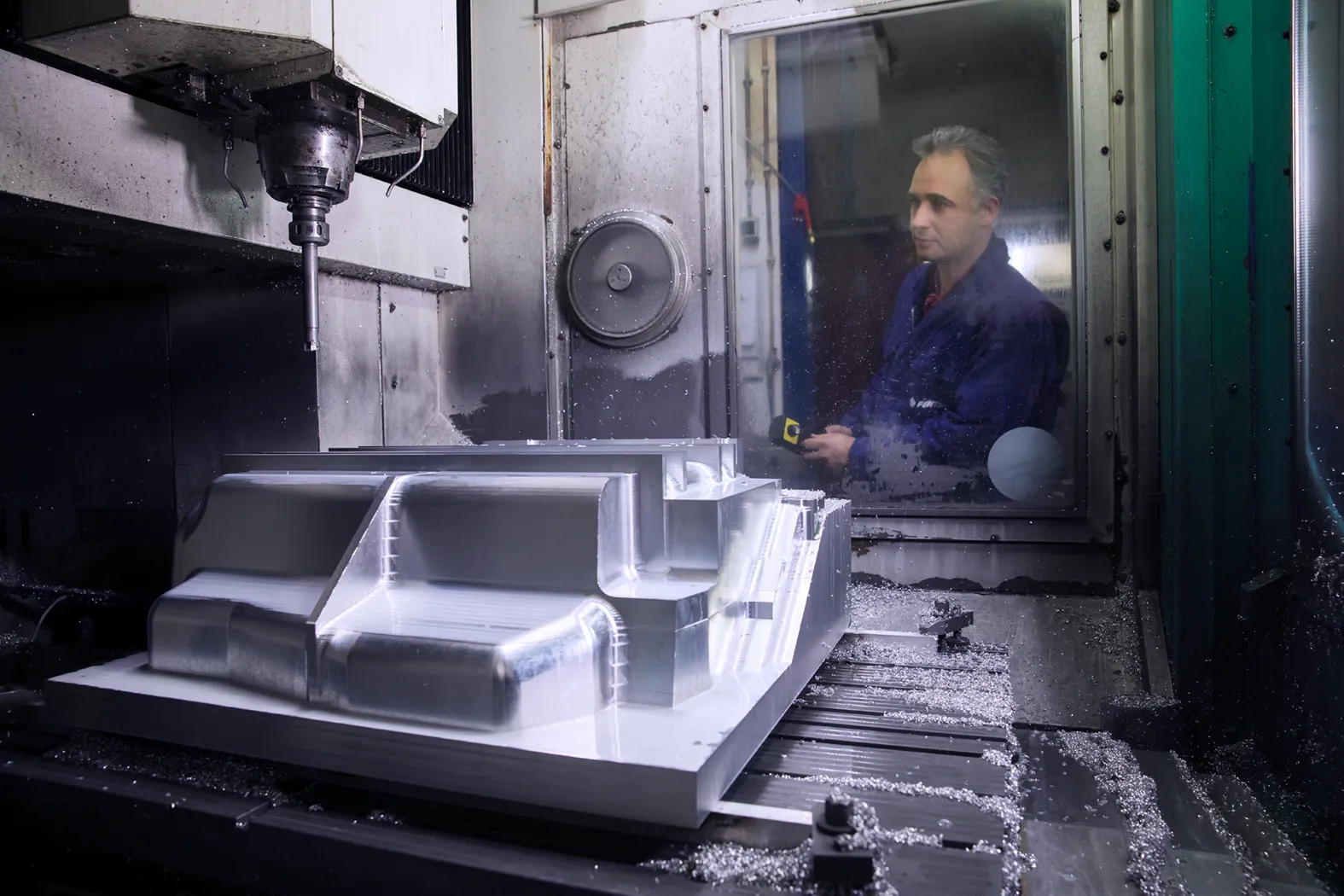
Rotational moulding is known as an advanced manufacturing process in which plastic powder is placed inside a mould. This mould is heated while rotating around two perpendicular axes. Due to this unique rotation, the plastic powder melts and evenly coats the inside of the mould. This results in a hollow product with a lot of design freedom regarding shapes and throughputs, something that is often difficult to achieve with other methods.
Mould Construction at Pentas
At Pentas, we design and construct our moulds ourselves. This is a logical choice, both for us and for the client. It starts with designing the product, from which a mould design follows. In designing the mould, considerations include undercuts, radii, demouldability, and heat management. Once we have gone through this process, we also design the frame/suspension of the moulds in 3D. Then, we start the physical work. Using advanced computer calculations, we create a milling program. This program is loaded into a CNC machine, which uses a rapidly spinning cutter to remove excess material from solid aluminium blocks, thus creating a thin aluminium wall in the shape of the product. We mill this from solid aluminium, allowing us to use the highest quality aluminium available in the market, which ultimately results in better and more durable moulds. This is a significant advantage over casting aluminium moulds.
Our CNC milling machines operate day and night, 7 days a week. This is a time-consuming process and can sometimes take weeks for the CNC machine to mill away aluminium. For large moulds, we opt to split them into smaller pieces; we mill these pieces separately to save on aluminium.
After milling all these pieces, the parts are assembled and welded by our mould builders. A frame is also constructed for mounting the mould on the machine. As a final step, the insides of the mould are polished and blasted, resulting in optimal surface quality of the final product. Thanks to this methodology, Pentas is capable of producing several moulds weekly.
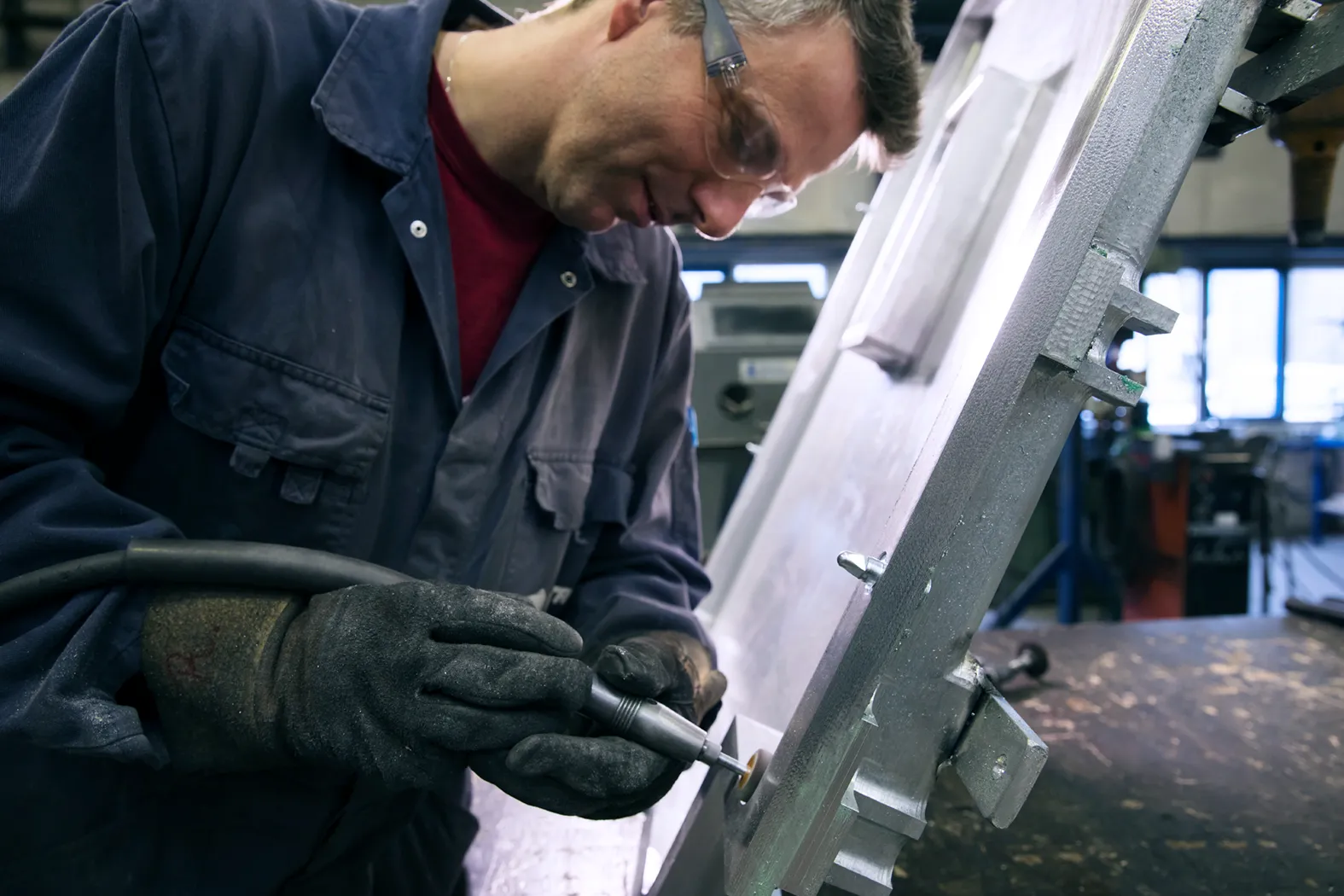
Material Choice
The choice of material for the mould in the rotational moulding process is crucial, as it greatly impacts both the efficiency of the manufacturing process and the quality of the final product. Aluminium is known for its excellent heat conduction, which is essential for even heat distribution during the moulding process. This ensures good melting and adhesion of the plastic material to the inside of the mould, resulting in high-quality products with consistent wall thicknesses. Moreover, aluminium is relatively easy to machine, facilitating the production of complex mould designs and simplifying adjustments or repairs.
Durability and Lifespan of the Mould
In selecting mould material, it's also important to consider factors like the mould's lifespan, the complexity of the part, and the total costs of the mould production process. While some materials may be more expensive initially, they can be more cost-effective in the long run due to their durability and lower maintenance requirements.
A well-maintained mould can last thousands of cycles, ensuring consistency and quality across long production runs.
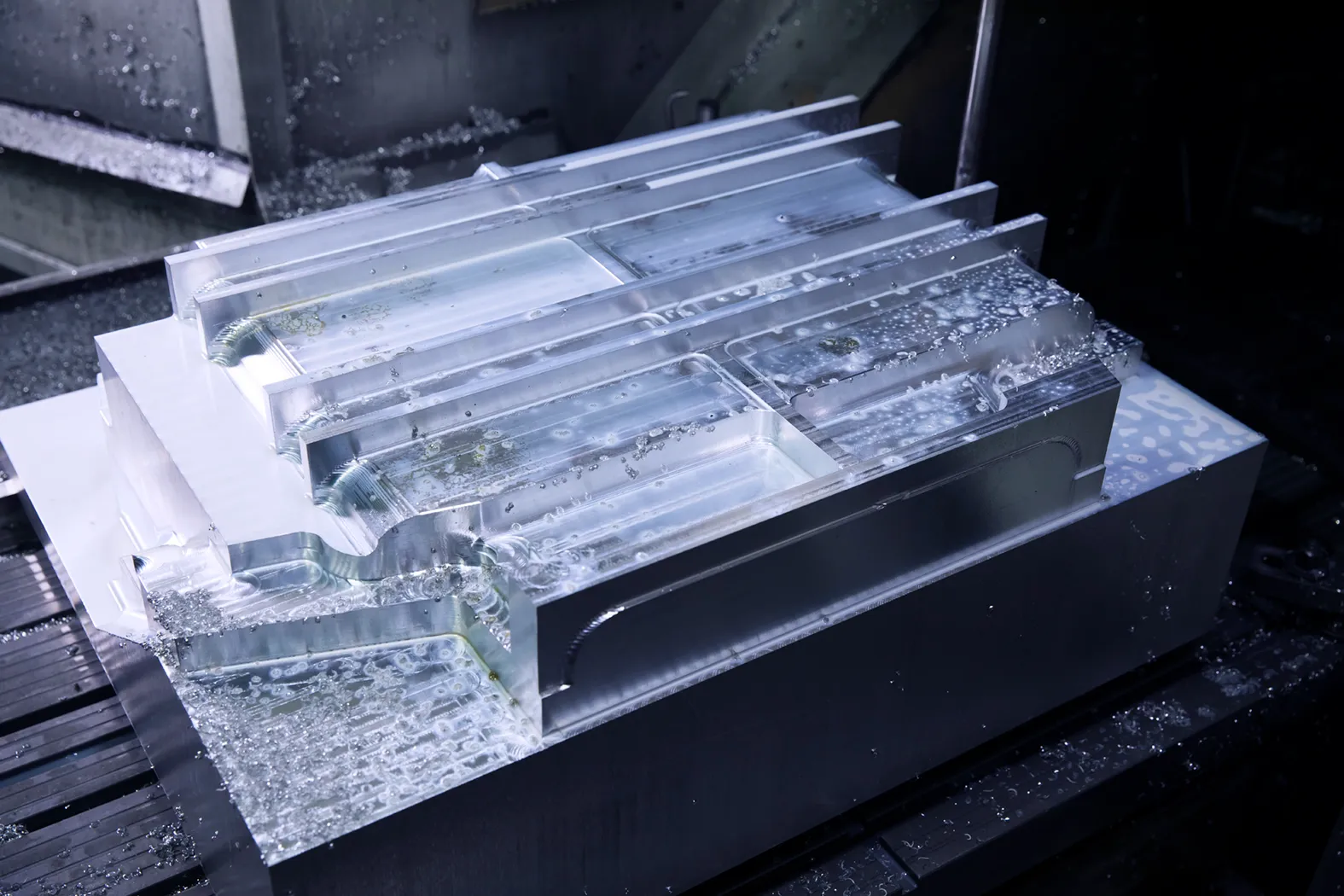
Technological Innovations
At Pentas, we have also recently started using a 3D scanner. Utilizing 3D scanning technology offers advantages in shaping moulds, particularly for products that require a realistic, natural look, such as textures of walls, sand, or tree bark. By digitizing these textures with a 3D scanner, we can integrate them into the 3D designs of the moulds. This leads to the production of end products with authentic surface textures that mimic natural shapes.
Mould construction at Pentas means that we have all the necessary resources in-house to serve the customer from start to finish. This distinguishes us and ensures that we are flexible and in control of our own scheduling. This allows us to respond quickly to customer needs.
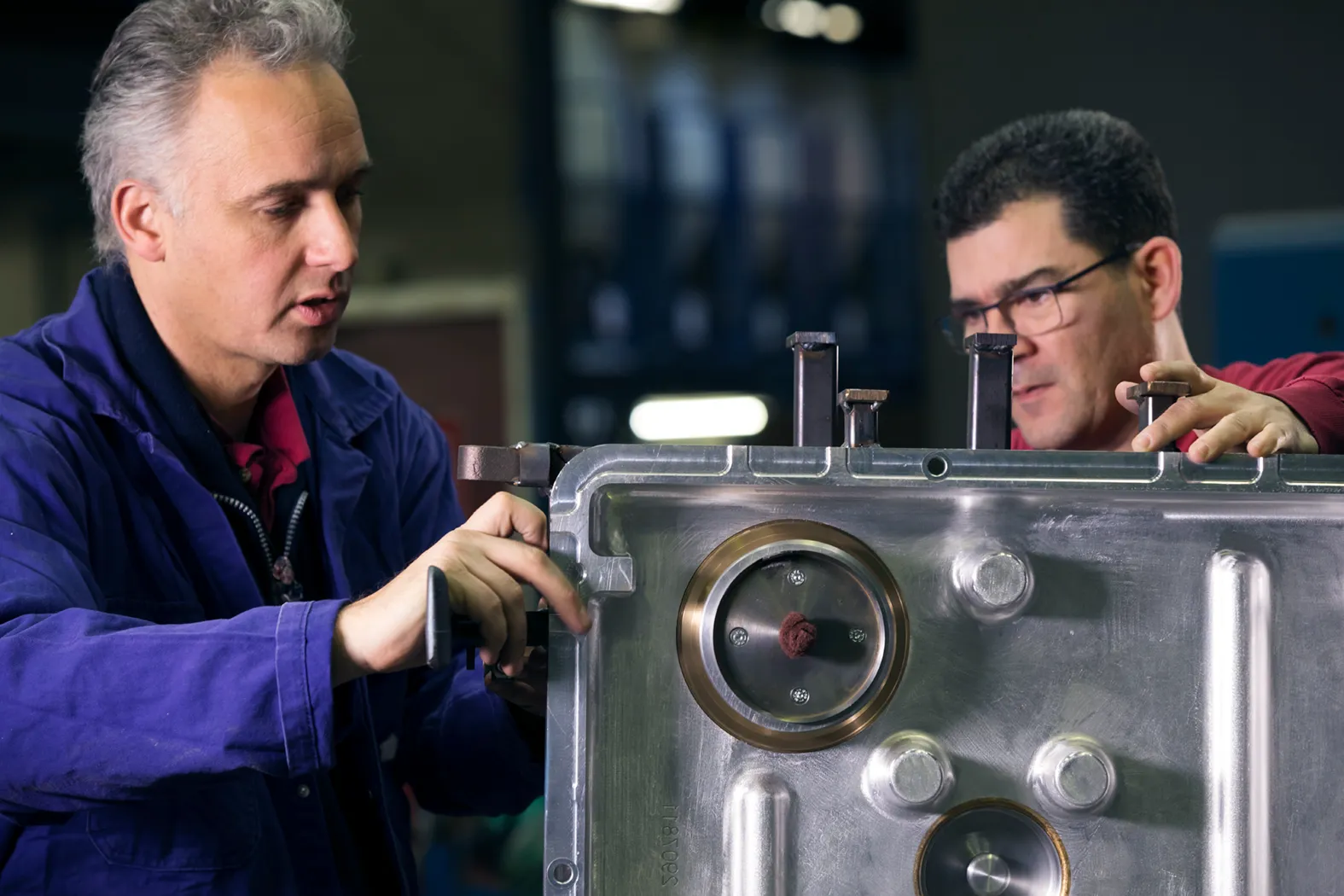
When adjustments to moulds are needed, we can act swiftly because the entire process takes place under one roof. This not only saves time but also reduces the risk of delays. The result is a smoother and faster process, allowing adjustments to be made with minimal interruptions. This ensures that we excel in customer service and provide a seamless experience, serving our customers well.