Rotational molding in the agricultural sector
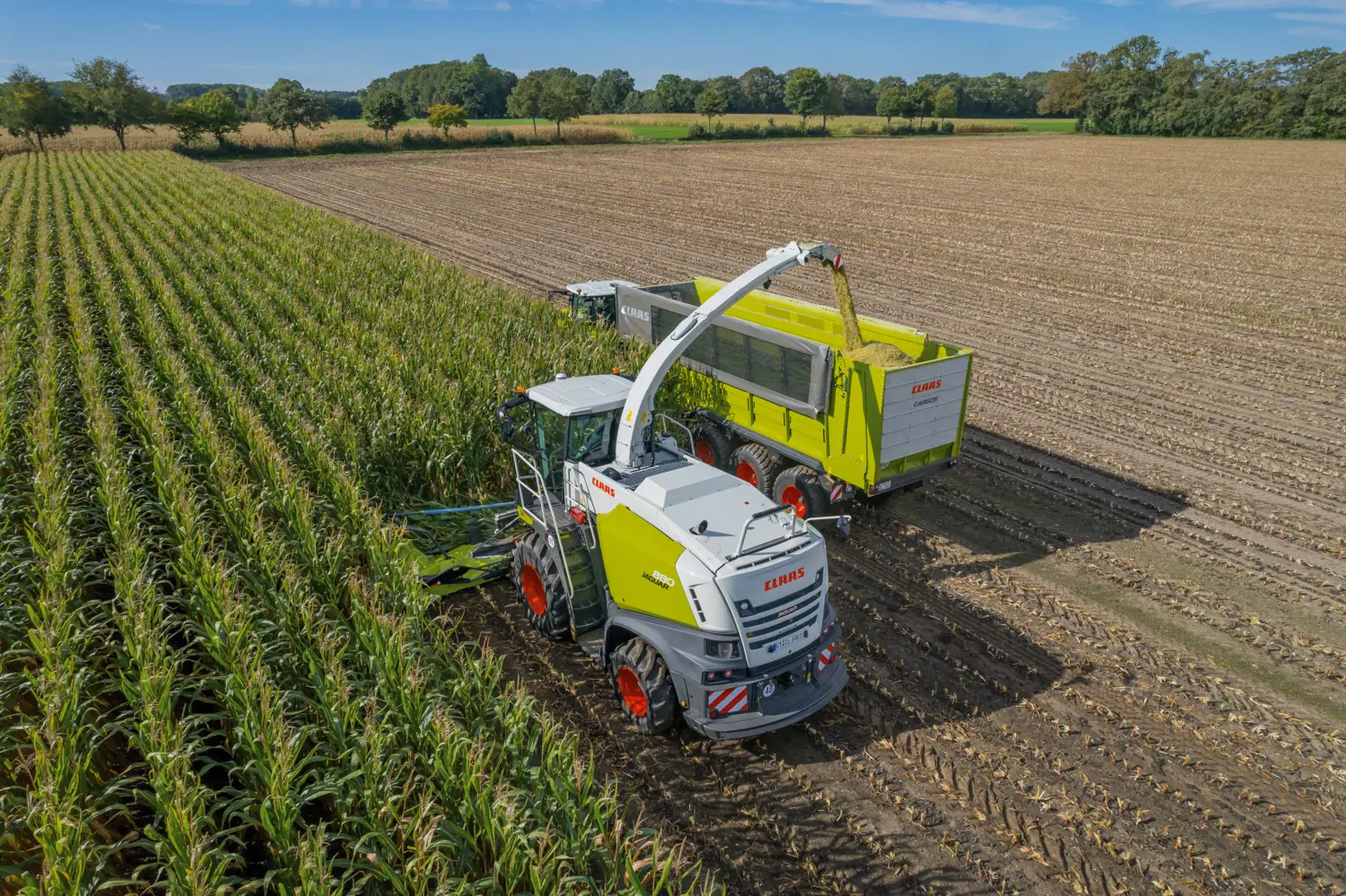
Rotational Molding is an essential method across various sectors. In this blog post, we'll discuss rotational molding and its application in producing tanks, fenders, and air ducts for agricultural machinery. To produce these parts and meet the high demands of the agricultural sector, expertise is needed.
Applications
Within the agricultural sector, products must not only meet high standards of strength, durability, and precision, but also be lightweight. This combination of requirements increases complexity and thus forms the core of the tension field. Rotational molding makes it possible to produce a wide range of products for agricultural machinery such as tanks, fenders, and air ducts. These products are indispensable and must withstand harsh conditions such as extreme weather, chemicals, and shocks/bumps during use.
Most products produced through rotational molding for agricultural machinery are made from polyethylene (PE), opting for the linear variant due to its good recycling properties. When producing products for the engine compartment (which are more subject to heat), polypropylene (PP) is often used.
Plastic Tanks
Developing plastic tanks, such as fuel tanks, urea tanks, and AdBlue tanks, is complex. Considerations must include regulations (with TÜV certificates being a requirement), the available space in the machine, and the forces acting on the tanks during use. With the experiences and knowledge of our engineers, we take all these factors into account when designing these tanks.
During the design process, consideration must also be given to integrating sensors and attachments, which are assembled to the tanks after rotational molding at Pentas. Thanks to our extensive network of suppliers for hoses, sensors, and caps, we can deliver a fully assembled tank of high quality. This way, the tank can be directly installed in the machine by the customer.
Fully assembled plastic tank with sensors.
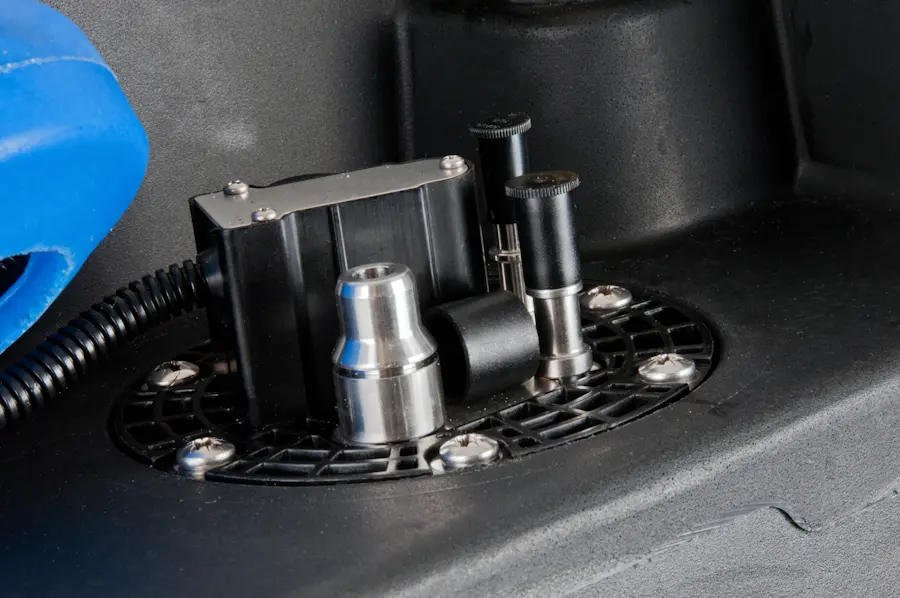
Before fuel tanks are allowed on public roads, they must be inspected. We have close ties with TÜV in Berlin, the organization that conducts these inspections. Here, tests such as a fire test, impact test, and material studies are conducted to ensure it's safe for such a tank to be on public roads.
Fenders
In addition to plastic tanks, our rotational molding process is perfectly suited for producing various types of fenders. These fenders are produced with double walls, making them extremely sturdy. Our production method allows for great shape freedom, enabling us to perfectly integrate fenders and seamlessly match the design of the machine. We produce fenders in all possible colors, for tractors, trailers, and similar machines. Often, reflectors and bumper strips are mounted on the fender afterward.
Employee working on the post-processing of a double-walled fender.
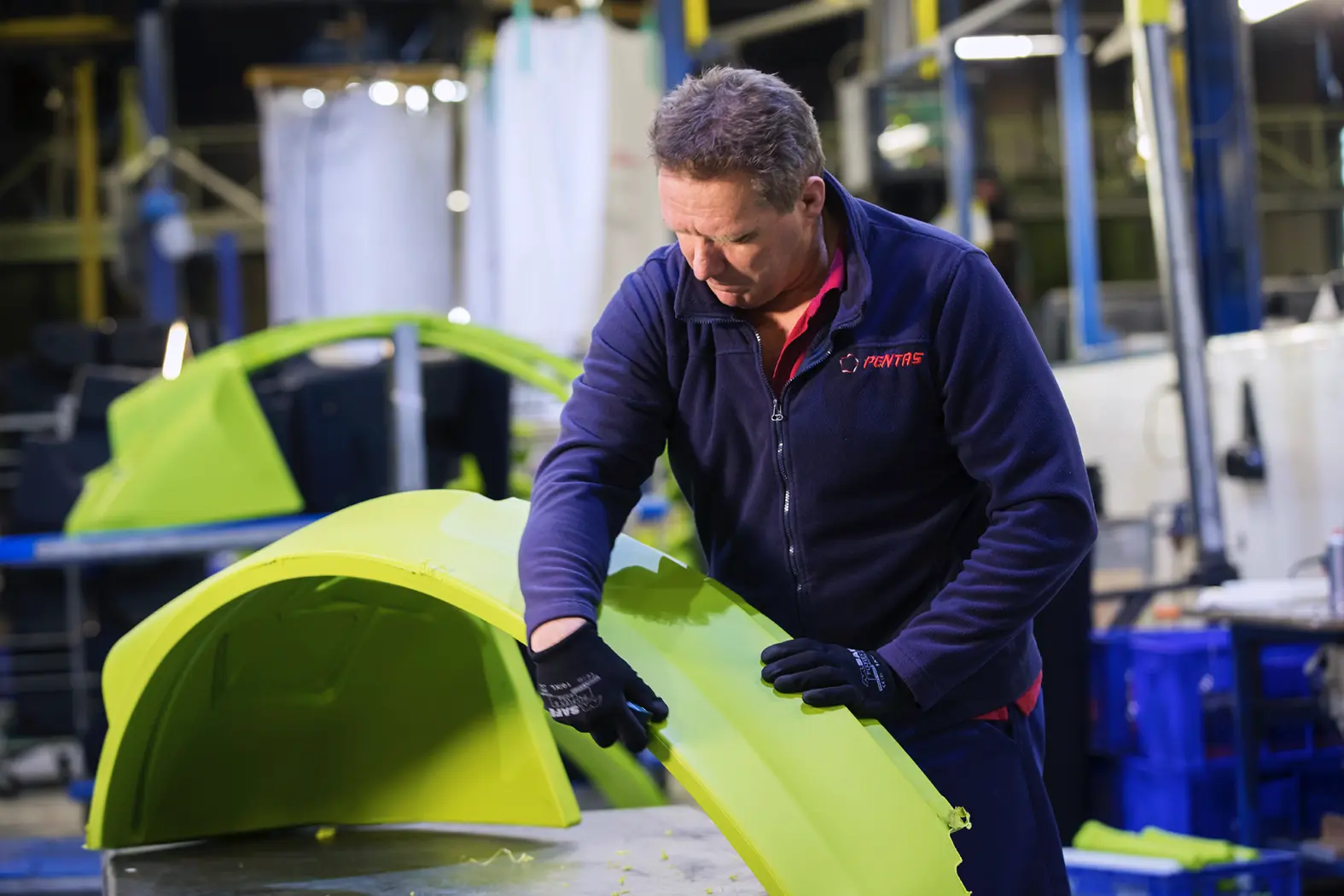
Air Ducts
Through rotational molding, we can develop plastic air ducts in the most challenging shapes with the most complex details, perfectly fitting within the allowable free space of agricultural machines. Because these often involve small air ducts, we can produce multiple products in one release using multiple molds. This allows us to offer the products cost-efficiently.
The air ducts are found in engine compartments and for air supply in the cabin. When the air duct is exposed to high temperatures, we use polypropylene (PP), a material that is difficult to process but very resistant to high temperatures. For this, we have developed special techniques with our raw material suppliers to properly process the material during rotational molding. The air ducts are post-processed with our ABB robot arms. These post-processing operations include milling openings and bending holes. We do this automatically to keep the tolerance small.
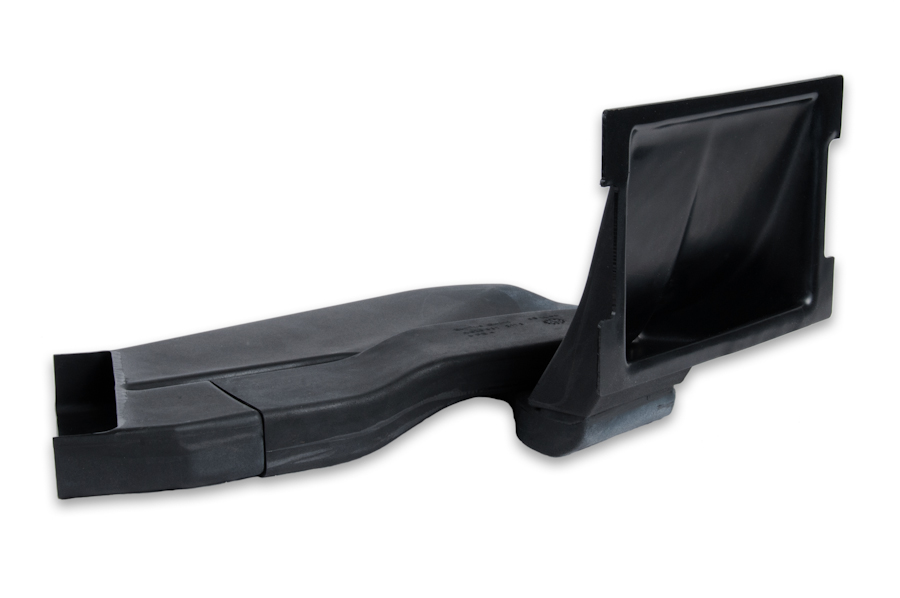
Production Process
At Pentas, every product starts with a design. We often design in collaboration with the customer's technical development department. We analyze the conditions in which the product must function, the allowed dimensions, and document everything. Together with the customer, we then design a product that meets these standards in terms of quality, efficiency, and durability. During our discussions with the customer, we bring a lot of experience and expertise to come to the best possible solution. Subsequently, we start designing the mold, a process that takes place internally at Pentas. This mold is crucial for the rotational molding process.
As soon as the first product comes out of the mold, an Initial Sample Inspection (ISI) is prepared. This document covers all critical dimensions and tests the product must meet. The product, in combination with the ISI document, is then presented to the customer for approval. After the customer's approval, mass production can begin.
Lighter Fuel Tanks for CLAAS
CLAAS asked us to develop a new design for the fuel tank of a combine harvester. These machines weigh a whopping 18 and 20 tons. Every kilogram we can save directly affects the ground pressure: the lighter the machine, the less pressure is exerted on the ground. This is crucial for crop growth. The environment also plays an important role; less material use is better. But of course, safety has the highest priority, so you have to balance between weight reduction and stability/strength.
To develop this lighter fuel tank, intensive creative sessions were held, various prototypes were tested using advanced computer simulations, and ultimately a solution was found that can be considered groundbreaking.
In collaboration with CLAAS, our engineers developed an innovative process that allows manufacturing fuel tanks with varying wall thickness at strategic locations. This results in a significant weight reduction of more than 25%, without sacrificing strength or functionality. This method, known as topology optimization, illustrates our continuous commitment to innovation and sustainability in product design.
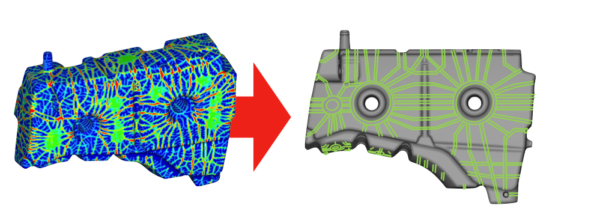
Pentas has specialized in the production of complex rotationally molded products for the agricultural sector for more than 25 years. Our long-standing experience and extensive expertise enable us to support our customers throughout the entire production process, from concept to finished product. We guarantee the highest quality in finishing, partly thanks to the use of advanced robot technologies. This commitment to efficiency and quality is crucial for the manufacture of agricultural machinery, where reliability and durability are paramount in the agricultural sector.
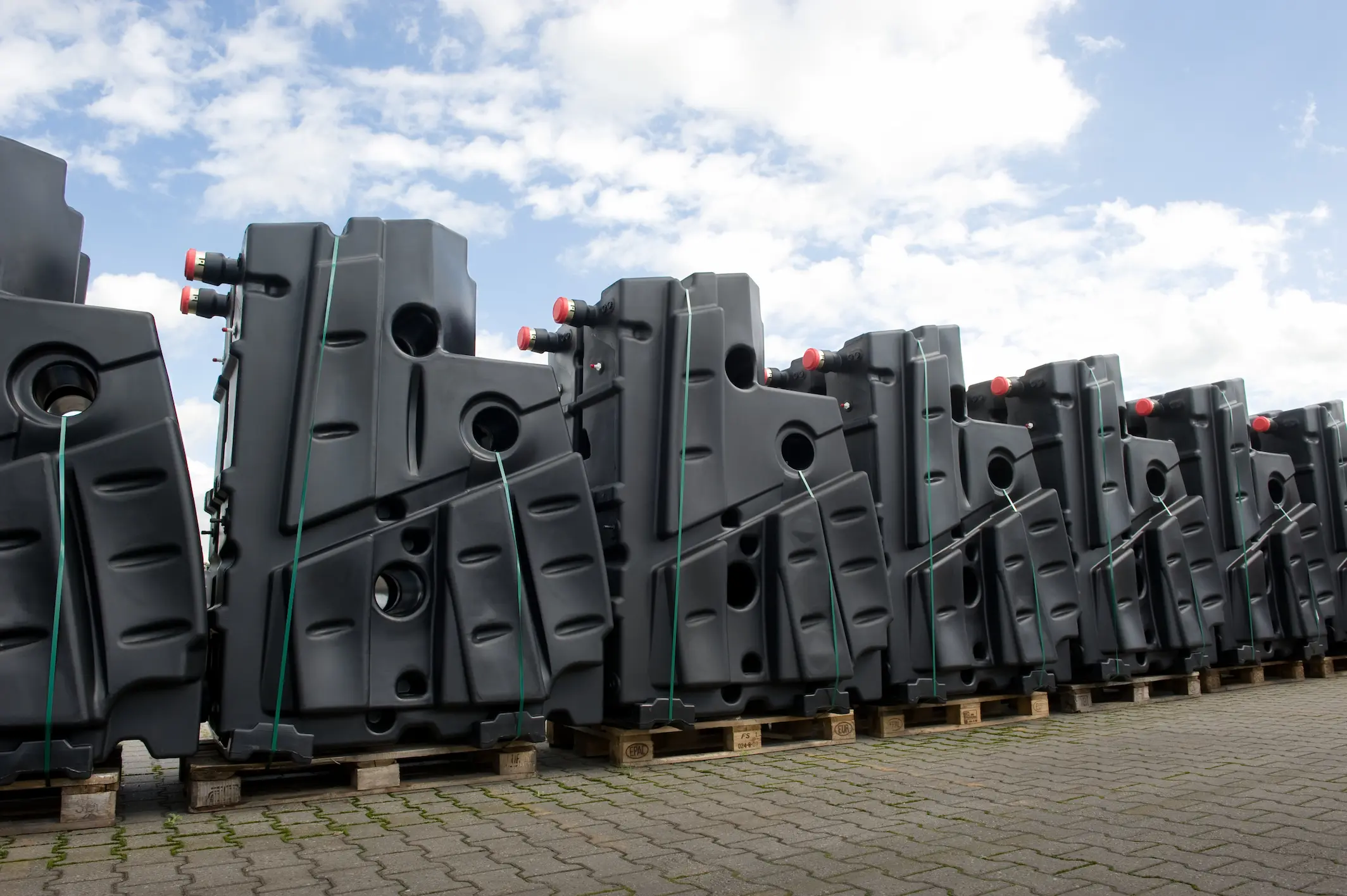